Pens! They just might be the cheapest, most important piece of technology ever overlooked by a large group of people on a daily basis. Pens are everywhere from your desk to your car to your junk drawer, though they tend to blink out of existence when you need one. Where would we be without them? Probably still drawing on cave walls with dandelions and beets.
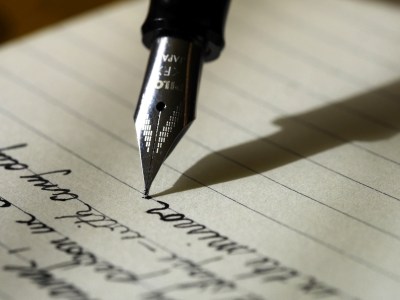
Why do I think pens are so great? Well, they’re a relatively cheap tool depending on the pen you get, but whatever you spend, you’re getting a lot for your money. Pens are possibility, pure and simple, and they’re even conveniently packaged in a portable device.
Aesthetically speaking, I like pens because of how different they can be both inside and out. Some of them make thick lines, some make thin lines, and in the case of flexible nibs, some alternate between thick and thin lines depending on pressure. I use pens for a number of reasons, most notably for writing. Everything you read here that bears my name began life as pen marks on paper.
Pens are revolutionary because they can be used to make ideas permanent and/or illustrate any concept. It’s up to you to use the pen wisely. You can use other, better tools later, but pens are always a great first tool. If you’re not encumbered by an uncomfortable grip, ink that skips, or a scratchy, draggy contact point, your ideas will flow more freely. When you find the right pen for you, you aren’t hindered by your tool — you’re elevated by it. Continue reading “A Few Of My Favorite Things: Pens”