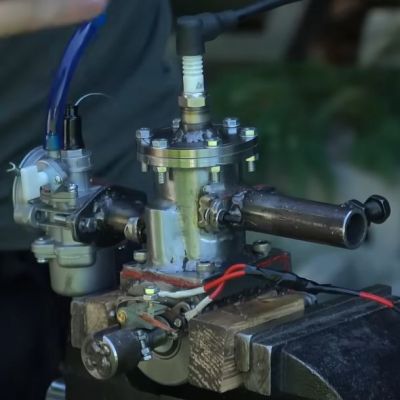
How hard could it to be to build a two-stroke internal combustion engine (ICE) from scratch? This is a challenge that [Camden Bowen] gladly set for himself, while foregoing such obvious wastes of time like first doing an in-depth literature study on the topic. That said, he did do some research and made the design in OnShape CAD before making his way over to the hardware store to make some purchases.
As it turns out, you can indeed build a two-stroke engine from scratch, using little more than some metal piping and other parts from the hardware store. You also need a welder and a lathe, with [Camden] using a Vevor mini-lathe that totally puts the ‘precision’ in ‘chatter’. As building an ICE requires a number of relatively basic parts that have to move with very little friction and with tight tolerances, this posed some challenges, but nothing that some DIY spirit can’t fix.
In the case of the very flexible boring bar on the lathe, improvising with some sturdy metal stock welded to a short boring bar resolved that, and precision was achieved. Together with an angle grinder, [Camden] was then able to manufacture the crank case, the cylinder and crank shaft and all the other pieces that make up an ICE. For the carburetor he used a unit off Amazon, which turned out to have the wrong throat size at 19 mm, but a 13 mm version worked. Ultimately, the first ICE constructed this way got destroyed mostly by running it dry and having the starter fluid acting as a solvent, but a full rebuild fixed all the issues.
This second attempt actually ran just fine the first time around, with oil in the crank case so that the poor engine wasn’t running dry any more. With a 40:1 fuel/oil mixture the little engine idles and runs as well as a two-stroke can, belching blue smoke and making a ruckus. This answers the question of whether you can build a two-stroke ICE with basic machining skills and tools, but of course the question that’s now on everyone’s lips is whether a four-stroke one would be nearly as ‘easy’. We wait with bated breath.
Continue reading “A Two-Stroke Engine Made From Scratch Using Basic Hardware Store Parts”