The Juno spacecraft was launched towards Jupiter in August of 2011 as part of the New Frontiers series of spacecraft, on what would originally have been a 7-year mission, including a nearly 5 year cruise to the planet. After a mission extension, it’s currently orbiting Jupiter, allowing for many more years of scientific data to be gathered using its instruments. One of these instruments is the JunoCam (JCM), a visible light camera and telescope. Unfortunately the harsh radiation environment around Jupiter had led many to believe that this camera would fail before long. Now it seems that NASA engineers have successfully tested a fix.
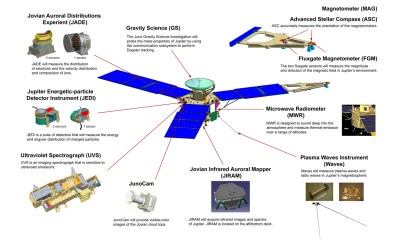
Although the radiation damage to JCM was obvious a few dozen orbits in – and well past its original mission’s 34 orbits – the big question was exactly what was being damaged by the radiation, and whether something could be done to circumvent or fix it. The good news was that the image sensor itself was fine, but one of the voltage regulators in JCM’s power supply was having a bad time. This led the engineers to try annealing the affected part by cranking up one of the JCM’s heaters to a balmy 25°C, well above what it normally is kept at.
This desperate step seemed to work, with massively improved image quality on the following orbits, but soon the images began to degrade again. Before an approach to Jupiter’s moon Io, the engineers thus tried it again but this time cranked the JCM’s heater up to eleven and crossed their fingers. Surprisingly this fixed the issue over the course of a week, until the JCM seems as good as new. Now the engineers are trying their luck with Juno‘s other instruments as well, with it potentially providing a blueprint for extending the life of spacecraft in general.
Thanks to [Mark Stevens] for the tip.