Useless robots (or useless machines) are devices that, when switched on, exist only to turn themselves back off. They are fun and fairly simple builds that are easy to personify, and really invite customization by their creators. Even so, [tobychui]’s Kawaii Useless Robot goes above and beyond in that regard. Not only will his creation dutifully turn itself off, but if the user persists in engaging it, Kawaii Useless Robot grows progressively (and adorably) upset which ultimately culminates in scooting about and trying to run away.
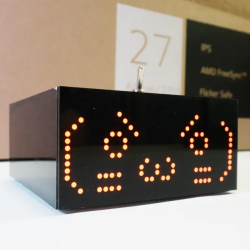
This is actually a ground-up re-imagining of an original work [tobychui] saw from a Japanese maker twelve years ago. That original Kawaii Useless Robot did not have any design details, so [tobychui] decided to re-create his own.
Behind the laser-cut front panel is a dot matrix LED display made up of eight smaller units, and inside are a total of four motors, an ESP32 development board, and supporting electronics. A neat touch is the ability to allow connections over Wi-Fi for debugging or remote control. The project page has some nice photos of the interior that are worth checking out. It’s a very compact and efficient build!
Watch it in action in the video (embedded below) which also includes a tour of the internals and a thorough description of the functions.
Inspired to make your own useless machine? Don’t be afraid to re-invent the whole concept. For example, we loved the one that physically spins the switch and the clock that falls to the floor when it detects someone looking at it. That last one is a close relative of the clock that displays the wrong time if and only if someone is looking.