Some people hate cables with a passion; others are agnostic and prefer cabled peripherals to having to stop and charge their mouse. [Matt] from DIYPerks has the best of both worlds with this wireless-powered, no-cable desk setup.
The secret is embedded within the plywood desk: an evaluation kit from Etherdyne Technologies, Inc consisting of a 100 W RF power supply and its associated power antenna looping around the desktop edge. The mechanism is similar to the inductive charging often seen on phones nowadays, but at higher frequency and larger scale, enabling power to be transmitted several feet (at least a meter) above the desktop.
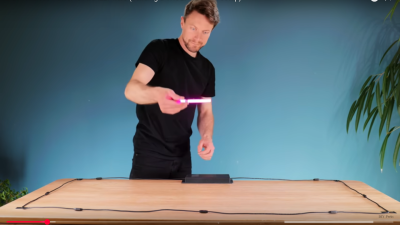
The kit from ETI contained several PCB-coil receivers, which [Matt] built into a number of devices, including a lamp, heated cup, microphone, speakers, his mouse, keyboard, and even a custom base to run his monitor, which really shows the power these things can pull.
The microphone is a non-Bluetooth RF unit lovingly modified to studio quality, at least as far as we can tell on laptop speakers through YouTube’s compression. The speakers use a pair of Bluetooth modules to negotiate stereo sound while staying in sync. And before you ask “what about signal for the monitor?”– we have to inform you that was taken care of too, via a wireless HDMI dongle. Check it out in the video below.
Of course the elephant in the room here is power usage — there’s a 10 W base draw, and probably a big hit to efficiency vs cabled-everything– but we figure he gets partway to a pass on that by using a Frameworks mainboard instead desktop hardware. Indeed, a full analysis might show that the transmission efficiency of this system is no worse than the power to charge/discharge inefficiencies in a more conventional battery powered wireless setup.
While no wires is pretty clean, we’re not sure this beats the totally-hidden-in-the-desk PC [Matt] built last year in terms of minimalist aesthetic. That Frameworks mainboard also likely lacks the power of his triple-screen luggable, but this was still an entertaining build.