Everyone loves to play with electricity and plasma, and [Hyperspace Pirate] is no exception. Inspired by a couple of 40×20 N52 neodymium magnets he had kicking around, he decided to put together a hand-cranked generator and use it to generate plasma with. Because that’s the kind of fun afternoon projects that enrich our lives, and who doesn’t want some Premium Fire™ to enrich their lives?
The generator itself is mostly 3D printed, with the magnets producing current in eight copper coils as they spin past. Courtesy of the 4.5:1 gear on the crank side, it actually spins at over 1,000 RPM with fairly low effort when unloaded, albeit due to the omission of iron cores in the coils. This due to otherwise the very strong magnets likely cogging the generator to the point where starting to turn it by hand would become practically impossible.
Despite this, the generator produces over a kilovolt with the 14,700 turns of 38 AWG copper wire, which is enough for the voltage multiplier and electrodes in the vacuum chamber, which were laid out as follows:
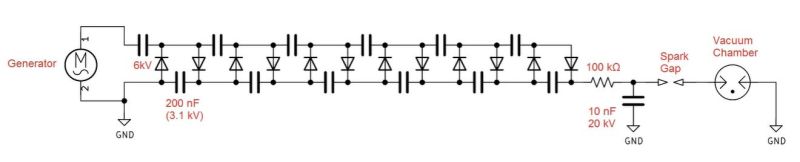
Some of our esteemed readers may be reminded of arc lighters which are all the rage these days, and this is basically the hand-cranked, up-scaled version of that. Aside from the benefits of having a portable super-arc lighter that doesn’t require batteries, the generator part could be useful in general for survival situations. Outside of a vacuum chamber the voltage required to ionize the air becomes higher, but since you generally don’t need a multi-centimeter arc to ignite some tinder, this contraption should be more than sufficient to light things on fire, as well as any stray neon signs you may come across.
If you’re looking for an easier way to provide some high-voltage excitement, automotive ignition coils can be pushed into service with little more than a 555 timer, and if you can get your hands on a flyback transformer from a CRT, firing them up is even easier.
Continue reading “Generating Plasma With A Hand-Cranked Generator”