Whilst designing hardware, it’s easy to shut the doors, close the blinds, and bury ourselves deeply into an after-hours design session. Although it’s tempting to fly solo, it’s likely that we’ll encounter bugs that others have handled, or perhaps we’ll realize that we forgot to add a handy feature that someone else could’ve noticed before we sent the darned PCB files out for fab. All that said, if we probe the community around us and ask for feedback, we can produce a project that’s far more functional and feature-complete in less time than if we were to design solo. Who knows? With enough eyes giving feedback on your project, maybe others will get excited enough to want one for themselves! [Andrew Werby] and [Zak Timan] on the FormLabs forums did just that: through months of iterative design and discussion on the FormLabs forums, they’ve created the first 3rd party glass resin tank that’s altogether sturdier, longer-lasting, more scratch-resistant, and less distorting than the original resin tank. And guess what? After months of trials through a few brave customers, you too can be the proud owner such a tank as they’re now up for sale on [Zak’s] website.
Continue reading “The Triumph Of Open Design And The Birth Of A FormLabs Aftermarket”
resin135 Articles
Fail Of The Week: Not All Mold Releases Release All Molds.
I’m writing a series of articles on resin casting as an extension to my experiences with the instructions found in the wonderful Guerrilla Guide. However, mistakes were made. Having run out of my usual mold release I went to a back-up jar that was lying around from a casting project long, long ago in a workshop far, far away.
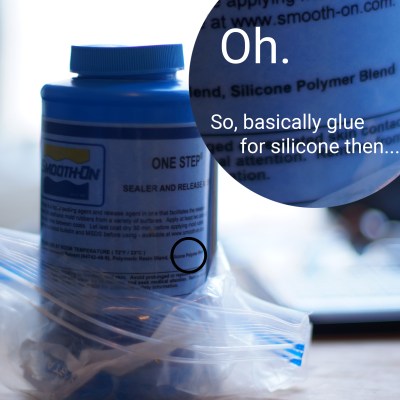
I’m refining a technique of making a mold the quick and dirty way. Everything was going well, the sprues looked good and the master released from the silicone. It was time to do the second half of the mold. As usual I applied a generous amount of mold release. Since it was the first time this mold was to be used I went ahead and did all the proper steps. Rubbing off the dried release and applying a few more coats just to be sure.
I was completely unaware that I was applying mold release designed for urethane molds only. In other words I thoroughly covered my silicone mold in silicone bonding agents. I remained unaware until trying to separate the halves of the mold and found them thoroughly joined. After going through the stages of grief I finally figured out where it all went wrong.
Oh well. I’m ordering some of my regular pick, Stoner A324, and that should do the trick. There’s also Mann- Ease Release 200. While having probably the best name a release agent can have, it doesn’t work as well and needs approximately 100 years to dry. After this setback I’d rather just, grudgingly, learn my lesson and order the correct thing.
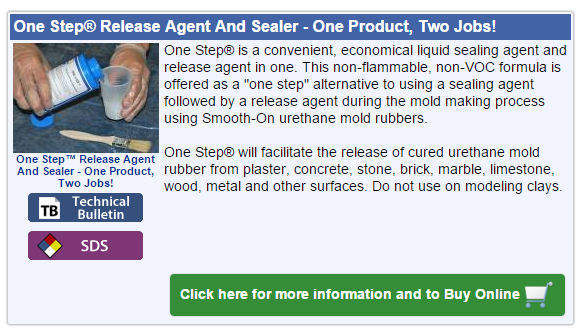
So now that we know the right way to fix this is to order the right product, is there a hack to get around it? Does anyone have a homebrew trick for release agent that can be used in a pinch? Leave your comments below.
Beer Kegs Make Excellent Resin Dispensers
[Josh Updyke] woke up one morning and found himself in a sticky situation. The demand for his modular robotic track system was outgrowing his ability to produce. One of the bottlenecks was weighing out resin. It’s a slow, monotonous process that must be done with accuracy. The free market did not have any affordable solutions to the problem. So like any hacker worth his weight in 2N2222 transistors, he made his own by re-purposing some used beer kegs.
The resin comes in two parts – the resin itself and a hardener. Each must be weighted out on a scale before mixing to ensure proper proportions. It was a trial-by-error learning process before [Josh] was able to settle on a final solution. First he tried some garden sprayers, which worked OK at first. But the resin was taking too long to exit the sprayers, and he had to pressurize them by manually pumping them with air. He ended up with a much better method that used some Cornelius Kegs.
Be sure to check out his io page for more details.
An Introduction To Casting With Nuka Cola
There’s less than a month until the next Star Wars is released, and consequently a few weeks until amateur propmakers and cosplayers go insane fabricating their own lightsabers with lightsaber cross guards and rolling robots. Until then, Fallout is pretty cool and [Bill] is here to give us an introduction to prop making with one of the defining objects of this post-apocalyptic universe. He created a real life copy of a Nuka Cola bottle and created a great introduction to resin casting in the process.
As with all proper part making endeavours, this project began with getting reasonably accurate models of the object to be copied. In Fallout, we’re lucky enough to have a way to look at a specific object while zooming and spinning around it, giving [Bill] the basic shape. The size was rather easy as well: all bottlecaps are the same size, so [Bill] just scaled the model to that.
With the model created and the part printed out, assembled, and finished, it was time to create the mold. [Bill] used a two-part silicone mold for the basic shape. The actual casting was done by rolling around a little resin on the inside of the mold. There’s no need for a solid, bottle-shaped block of resin; bottles are hollow anyway.
There are a few neat tricks [Bill] has up his sleeve, including coating the inside of the mold with aluminum powder and using a vinyl cutter to get the labels and logos exactly right. The finished product turns out great, perfect for leaving in the Wasteland for 200 years until the Sole Survivor stumbles upon it.
Video below.
Continue reading “An Introduction To Casting With Nuka Cola”
3D Printed Eyeglasses, VR Lenses
[Florian] is hyped for Google Cardboard, Oculus Rifts, and other head mounted displays, and with that comes an interest in lenses. [Floian] wanted to know if it was possible to create these lenses with a 3D printer. Why would anyone want to do this when these lenses can be had from dozens of online retailers for a few dollars? The phrase, ‘because I can’ comes to mind.
The starting point for the lens was a CAD model, a 3D printer, and silicone mold material. Clear casting resin fills the mold, cures, and turns into a translucent lens-shaped blob. This is the process of creating all lenses, and by finely sanding, polishing, and buffing this lens with grits ranging from 200 to 7000, this bit of resin slowly takes on an optically clear shine.
Do these lenses work? Yes, and [Florian] managed to build a head mounted display that can hold an iPhone up to his face for viewing 3D images and movies. The next goal is printing prescription glasses, and [Florian] seems very close to achieving that dream.
The last time we saw home lens making was more than a year ago. Is anyone else dabbling in this dark art? Let us know in the comments below and send in a tip if you have a favorite lens hack in mind.
Tint Your Epoxy Resin With Toner Powder
Epoxy resin is useful stuff. Whether for gluing stuff together or potting components, epoxy is a cheap and versatile polymer that finds its way into many hackish projects. But let’s face it – the stock color of most commercially available epoxies lacks a certain pizzazz. Luckily, [Rupert Hirst] at Tallman Labs shows us that epoxy is easily tinted with toner powder from a laser printer or copier.
Looking for a way to make his epoxy blend into a glue-up, [Rupert] also demonstrates that colored epoxy makes a professional looking potting compound. There’s just something about the silky, liquid look of a blob of cured black epoxy. [Rupert] harvested his toner powder from a depleted printer cartridge; only a smidgen is needed, so you should be able to recover plenty before recycling the cartridge. We’ve got to admit that seeing toner handled without gloves gives us the willies, though. And don’t forget that you can find cyan, magenta and yellow cartridges too if basic black isn’t your thing.
Sometimes it’s better to leave your epoxy somewhat clear, like when you’re potting an LED matrix for a pendant. But this neat trick might just spiff up your next project a bit.
[Thanks, Jake]
3D Printering: Maker Faire And Resin Printers
Of course Maker Faire was loaded up with 3D printers, but we’re no longer in the era of a 3D printer in every single booth. Filament-based printers are passé, but that doesn’t mean there’s no new technology to demonstrate. This year, it was stereolithography and other resin-based printers. Here’s the roundup of each and every one displayed at the faire, and the reason it’s still not prime time for resin-based printers.
Formlabs
Of course the Formlabs Form 1+ was presented at the Bay Area Maker Faire. They were one of the first SLA printers on the market, and they’ve jumped through enough legal hoops to be able to call themselves the current kings of low-cost laser and resin printing. There were a few new companies and products at the Faire vying for the top spot, and this is where things get interesting.
The folks at Formlabs displayed the only functional print of all the resin-based 3D printing companies – a tiny, tiny Philco Predicta stuffed with an LCD displaying composite video. The display is covered by a 3D printed lens/window. That’s the closest you’re going to get to an optically clear 3D printed part at the Faire.
XYZPrinting Nobel
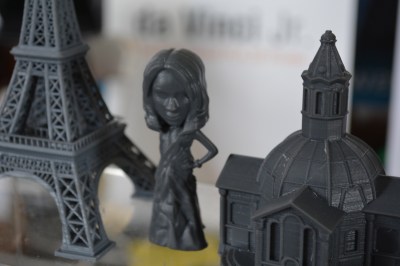
XYZPrinting, the company famous for the $500 printer that follows the Gillette model: sell the printer cheap, sell expensive replacement filament cartridges, and laugh all the way to the bank. Resetting the DRM on the XYZPrinting Da Vinci printer is easy, the proprietary host software is done away with, and bricked devices are not. Time for a new market, huh?
Enter the XYZPrinting Nobel, a resin printer that uses lasers to solidify parts 25 microns at a time. The build volume is 125x125x200mm (5x5x7.9″), with an X and Y resolution of 300 microns. Everything prints out just as you would expect. As far as laser resin printers go, it’s incredibly cheap: $1500. It does, however, use XYZware, the proprietary toolchain forced upon Da Vinci users, although the Nobel is a stand-alone printer that can pull a .STL file from a USB drive and turn it into an object without a computer. There was no mention of how – or if – this printer is locked down.
DWS Lab XFAB
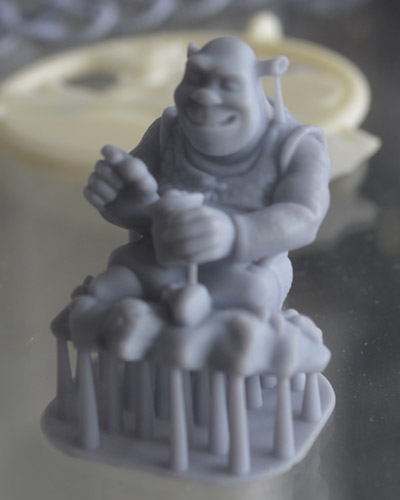
You’ve seen the cheapest, now check out the most expensive. It’s the DWS Lab XFAB, an enormous and impressive machine that has incredible resolution, a huge build area, and when you take into account other resin printers, a price approaching insanity.
First, the price: $5000 officially, although I heard rumors of $6500 around the 3D printing tent. No, it’s not for sale yet – they’re still in beta testing. Compare that to the Formlabs Form 1+ at $3300, or the XYZPrinting Nobel at $1500, and you would expect this printer to be incredible. You would be right.
The minimum feature size of the XFAB is 80 microns, and can slice down to 10 microns. Compare that to the 300 micron feature size of the Form 1+ and Nobel, and even on paper, you can tell they really have something here. Looking at the sample prints, they do. These are simply the highest resolution 3D printed objects I’ve ever seen. The quality of the prints compares to the finest resin cast objects, machined plastic, or any other manufacturing process. If you’re looking for a printer for very, very high quality work, this is what you need.
Sharebot Voyager
Also on display – but not in the 3D printing booth, for some reason – was the Sharebot Voyager. Unlike all the printers described above, this is a DLP printer; instead of lasers and galvos, the Voyager uses an off-the-shelf 3D DLP projector to harden layers of resin.
Strangely, the Sharebot Voyager was stuck in either the Atmel or the Arduino.cc (the [Massimo] one) booth. The printing area is a bit small – 56x96x100mm, but the resolution – on paper, mind you – goes beyond what the most expensive laser and galvo printers can manage: 50 microns in the X and Y axes, 20 to 100 microns in the Z. Compare that figure to the XFAB’s 80 micron minimum feature size, and you begin to see the genius of using a DLP projector.
The Sharebot Voyager is fully controllable over the web thanks to a 1.5GHz quad core, 1GB RAM computer that I believe is running 32 bit Windows. Yes, the spec sheet said OS: 32 bit Windows.
There were no sample prints, no price, and no expected release date. It is, for all intents and purposes, vaporware. I’ve seen it, I’ve taken pictures of it, but I’ve done that for a lot of products that never made it to market.
The Problem With Resin Printers
Taking a gander over all the resin-based 3D printers, you start to pick up on a few common themes. All the software is proprietary, and there is no open source solution for either moving galvos, lasers, or displaying images on a DLP projector correctly to run a resin-based machine. Yes, you heard it here first: it’s the first time in history Open Source hardware folk are ahead of the Open Source software folk. Honestly, open source resin printer hosts is something that should have been done years ago.
This will change in just a few months. A scary, tattooed little bird told me there will soon be an open source solution to printing in resin by the Detroit Maker Faire. Then, finally, the deluge of resin.