These days it’s hard to not come across solid-state (micro-electromechanical systems, MEMS) microphones, as they are now displacing electret microphones almost everywhere due to their small size and low cost. Although MEMS speakers are not impossible, creating a miniature speaker that can both displace a lot of air (‘volume’) and accurately reproduce a wide range of frequencies – unlike simple piezo buzzers – is a lot tougher. Here a startup called xMEMS figures that they have at least partially cracked the code with their piezoMEMS speakers, with Creative using the Cowell version in their brand-new Aurvana Ace in-ear monitors. Continue reading “After MEMS Microphones, MEMS Speakers Enter The Market”
digital audio hacks725 Articles
Stream Vinyl To Your Sonos Without The Financial Penalty
One of the unexpected success stories in the world of hi-fi over the past decade has been the resurgence of the vinyl LP as a musical format. What was once old hat is now cool again, but for freshy minted vinyl fans there’s a snag. Hi-fi itself has moved on from the analogue into the digital, so what can be done if your listening comes through a Sonos system. Sonos will sell you a box to do that of course, but it’s as overpriced as 2023-pressing vinyl. [Max Fischer] has a far better solution, in the form of a Raspberry Pi loaded with open source software.
At the vinyl end is a Behringer audio interface containing a pre-amp with the required RIAA response curve. This acts as the source for the DarkIce audio streamer and the IceCast2 media serer, all of which even with the cost of a Pi and the interface, is considerably less than the commercial device.
We’re guessing that a more humble interface coupled to an older RIAA pre-amp could cut the cost further, and we’d be hugely curious as to whether a simple mic pre-amp could be used alongside some DSP from the likes of Gnu Radio to give the RIAA response.
Either way, he’s made a handy device for any 21st-century vinyl fan. Meanwhile if you’re one of the streaming generation seduced by round plastic discs, we’ve gone into some detail about their audiophile credentials in the past. And if you have found yourself a turntable, of course you’ll need to know how to set it up properly.
The Best-Sounding Walnut You’ll Hear Today
Do you ever find yourself eating walnuts and think, this would make a great enclosure for something like a Bluetooth speaker? That seems to be exactly what happened to [Penguin DIY].
In the mesmerizing video after the break, you’ll see [Penguin DIY] do what seems to be impossible. They start with a tiny 5 V power bank module which is still not small enough to fit, so they remove all the components and dead-bug them back together.
This is really just the beginning. There of course has to be a female USB of some type, so [Penguin DIY] Dremels out the perfect little slot for it.
They did manage to stack and fit a MH-MH18 Bluetooth audio module and an HXJ8002 mini audio amplifier module in the walnut, but of course, it took a lot of fiddly wiring to extend the LEDs and wire them up.
Then in the other half of the shell went the 4Ω 2 W mini speaker. [Penguin DIY] of course drilled a ton of little holes in the shell for the sound to come through. Also on this side are three tiny switches for play/pause and previous and next track, and the latter two can be long pressed to control the volume. Definitely check this out after the break.
Do the notifications of your Bluetooth speaker annoy you? There’s a hack for that.
Continue reading “The Best-Sounding Walnut You’ll Hear Today”
Exploring Hidden Lyrics On 1990s DCC Audio Tapes
Having a fondness for old and obscure audio and video media formats, [Techmoan] recently revisited the Philips Digital Compact Cassette (DCC) format introduced in 1992. Despite being billed as the successor to Philips’ original analog Compact Cassette format from 1963, DCC was short-lived and slipped away after only four years in 1996. [Techmoan] obtained a unique cassette that purports to be the only known published DCC tape which contains embedded song lyrics that scroll on the DCC player’s tiny screen in sync with the music — “Size Isn’t Everything” by the Bee Gees from 1993. Sure enough, he is able to demonstrate this in the video down below the break.
But, there’s more. For reasons unclear, this only happens on on this one Bee Gees’ album. But it turns out that many DCC tapes did in fact include lots of other metadata, and sometimes lyrics as well. But these were only visible using an unreleased Philips system called Interactive Text Transmission System (ITTS). It just so happens that the folks at the DCC Museum obtained a Philips prototype ITTS box and have been gradually hacking the protocol.
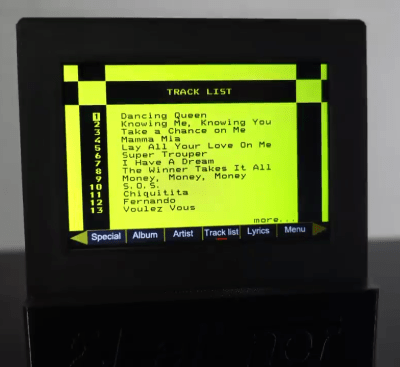
[Techmoan] demonstrates a modernized prototype version from Germany designed by [Thomas Falkner] called the ITTS video box NG. Using this, he runs through a bunch of DCC tapes from his collection, and finds a significant number of them were published with lyrics and metadata, presumably in anticipation of as ITTS launch. It’s interesting to see how some publishers spent a lot of effort to format this information and others seemed to just copy / paste over the bare minimum.
The more elaborate pages resemble what you might see on your teletext screens back in the day. On those albums that do have lyrics, the presentation can be different, as well. Lyrics from the Bee Gees album appear like text scrolling up on a terminal, with current phrases shown in yellow. Another album’s lyrics can be scrolled in different peculiar ways, including a one-word-at-a-time mode.
If this kind of historical dive into technology interests you, check out the talk that [Jac] and [Ralf] gave at the 2022 Supercon about DCC, and this video from 2018 where [Ralf] digs deeper into this topic. Also, [Jac] has some more recent details on hacking the protocol posted over on his Hackaday.io project page. If you want a more basic introduction to DCC, [Techmoan] introduced this format some years ago on his YouTube channel.
Continue reading “Exploring Hidden Lyrics On 1990s DCC Audio Tapes”
Fixing Some More Of Apple’s Design Mistakes
Love them or hate them, there’s no denying that Apple has strayed from the Woz’s original open platform ideal for the Apple II. [Ken Pillonel] is back for another round of fixing Apple’s repairability mistakes with a full complement of 3D printable replacement parts for the AirPods Pro case.
While modeling all of the parts would be handy enough for repairing a device with a 0/10 iFixit score, [Pillonel] modified the parts to go together with screws instead of adhesive so any future repairs don’t require cracking the plastic egg. He says, “By showcasing the potential for repairability, I hope to inspire both consumers and multi-billion dollar companies, like Apple, to embrace sustainable practices in their products.”
[Pillonel]’s repairability exploits may seem familiar to readers from his previous work on adding USB-C to the iPhone and the AirPods Pro case. If you just need to retrieve a lost AirPod, you might try an electromagnet, or you can make a Bluetooth receiver from a pair of knock-off buds.
Continue reading “Fixing Some More Of Apple’s Design Mistakes”
Planar Speaker Build Uses Hard Drive Magnets
We like to see people building things that are a little unusual, and we really like it when said unusual thing uses salvaged parts. This project from [JGJMatt] ticks all our boxes — the build creates a planar speaker that uses salvaged magnets from a hard drive.
A planar speaker, according to the post, uses wires and magnets to manipulate a flat film that acts as the transducer. The speaker housing is 3D printed and looks great but is otherwise unremarkable. The fun starts when a Dremel with a diamond disk cuts the magnets in half. Cutting neodymium poses several challenges. For example, if you heat the material up too much while cutting, it can lose its magnetism.
With the proper magnets, you can move to the tedious method of creating the coils. The post shows three different methods. But the part we really liked was using a resin 3D printer as a UV source to expose a resist mask which transfers to a copper or aluminum foil that will be the sound-generating film. [JGJMatt] used a similar technique to put resist on PC board blanks, too. Unfortunately, there were some issues so the finished speakers didn’t use the foil prepared using this method. Instead, a quick modification to the resin printer allowed a thin film of resin to rest on the foil, which was then exposed.
Once you have the pieces, there isn’t much left to do but put them together. Honestly, this is one of those things you probably won’t do yourself unless you are obsessed with speakers. But there were a lot of interesting techniques here that might come in handy, even if you don’t care about audio reproduction.
[JGJMatt] showed us a ribbon speaker before. We have seen some speakers that are practically all 3D printed.
IKEA Hack – Kvart Into Mic Stand
While audiophiles might spend gazillions of hours finely honing a microphone stand that isolates their equipment from the trials and perturbations of the world, most of us who use a microphone don’t need anything so elaborate. Hackaday contributing editor [Jenny List] hacked together some thrift store finds into a snazzy adjustable mic setup as you can see in the video below the break.
Using the flexible neck and clamp of an IKEA Kvart as a base, [Lists]’s mic stand looks like a simple, but exceedingly useful tool. She first removed the lamp, shade, and cord before designing a 3D-printed mount to attach to the lamp’s neck. Since the bolted lamp end of the connection goes straight to an action camera mounting system, we can see this being handy for mounting any number of other things besides microphones. Another 3D-printed mount attaches the Logitech gaming microphone to the action camera connector, and the whole thing can either be bolted together or use a printed pin. All the parts can be found in a GitHub repository.
Looking for more microphone hacks? Check out this DIY ribbon microphone or the Ambi-Alice ambisonic mic.