For many DIY hardware projects, the most movement it’s likely to see is when we pick the assembled unit up off the workbench and carry it to wherever it’s destined to spend the rest of its functional life. From weather sensors to smart mirrors, there’s a huge array of devices that don’t need to move one millimeter to function. But eventually, you’re likely to run into a project that’s a bit more dynamic. Maybe you’d like to motorize your window shades, or go all out and build a remote controlled rover. With these more active designs comes a whole slew of new problems you may never have encountered before.
Luckily for us, folks like Jeremy Fielding are out there and willing to share their knowledge. In his fascinating presentation for the 2021 Hackaday Remoticon, Building Hardware that Moves: the Fundamentals that Everyone Should Know, he took viewers on a whirlwind tour of what he’s learned about designing and building complex machines from his years of professional experience. Whether its a relatively simple articulated workbench for the shop, a gargantuan earthmoving machine, or a high-dexterity robotic arm, each project he’s worked on has presented unique challenges that needed to be solved.
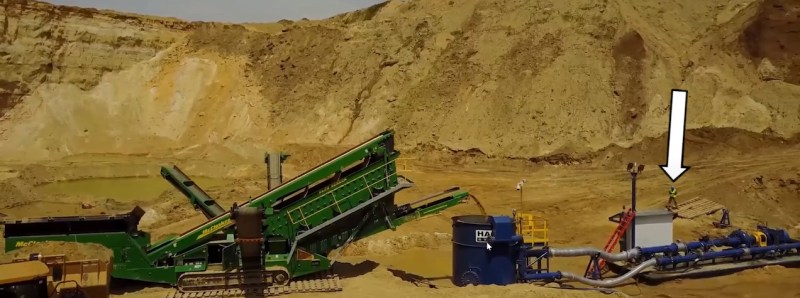
A lot of the projects that Jeremy has worked on are on a much larger scale than what your average hobbyist is ever going to run into. When there’s an arrow pointing out the tiny human in a picture of you and the machine you’re currently working on, you know things are getting serious. But as anyone who’s watched his YouTube videos knows, he’s got a real knack for taking these high-level concepts and distilling them into something more digestible for the home gamer.
Continue reading “Keynote Video: Jeremy Fielding Wants To Help You Get Moving”