As useful as electronics are, the need to have some source of power for them can be a bit of an issue, especially for small, portable devices. One of the most low-tech but universally applicable source is human mechanical power, as demonstrated by the rugged 1980s-era Messenger II tape player in a recent [TechMoan] video. Without beating around the bush, this is indeed a device created by an evangelical organization (GRN) that missionaries would take with them to wherever their mission took them. Naturally this put the availability of power from a wall outlet in question, especially in the 1980s when this tape player was produced. Continue reading “Ready For The Rapture: This Wind-Up Cassette Player Can Play Anywhere”
hand crank5 Articles
Printed Axial Generator Is Turned By Hand
While desktop 3D printing is an incredible technology, it’s got some pretty clear limitations. Plastic parts can be produced quickly in a 3D printer but can be more expensive or take longer to make than parts from materials like wood. Plastic parts can also be weaker than materials like metal. If a 3D printer is all you have on hand, though, you can often make some design choices that improve the performance of a plastic part over other materials. That’s what [1970sWizard] did to make this axial hand-cranked generator.
Besides a few pieces of off-the-shelf hardware and the wire and magnets, the entire generator is printed. The actual generator is made from coils of wire with exposed leads which snap into a plastic disc which acts as the generator’s stator. The magnets also snap into a separate disc which is the rotor of the generator and is attached to the drivetrain, with no glue or fasteners required. A series of gears on two other axes convert the torque from the hand crank into the high speed necessary to get usable electricity out of the generator.
The separate gear shafts were necessary to keep from needing a drillpress, which would have allowed fewer axes to be used. This entire machine can be built almost entirely with a desktop 3D printer, though, which was one of the design goals. While it’s largely a proof-of-concept, the machine does generate about 100 mW of power which is enough to slowly charge USB devices, power lights, or provide other sources of very small amounts of energy. If you do have access to some metalworking tools, though, take a look at this hand-cranked emergency generator.
Continue reading “Printed Axial Generator Is Turned By Hand”
7000 RPM On A 3D-Printed Gearbox
[Steven] at the 3D Printer Academy has been working on a variety of different gear designs. He recently embarked on a series of experiments to see how fast he can spin a 3D-printed gearbox.
After testing several kinds of gear teeth, gear diameters, and gear spacing, he finally struck upon an 81:1 ratio gearbox. It has six gears: five stepped gears and one drive gear on the input shaft. First tests are accomplished with a 3D-printed handle, similar to a hand crank used to start really old cars. But unlike those cranks, [Steven]’s doesn’t have any release provision. While the handle can be removed, it can’t be removed while spinning.
We think it would be helpful to revise the drive shaft coupling method, allowing the handle or drill to be easily removed from the gearbox once it’s attained speed. This would be more convenient, and it seems prudent from the workbench safety point of view as well.
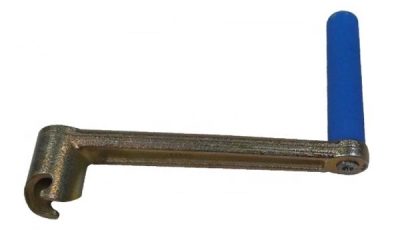
[Steven] manages to get the final gear spinning at 7000 RPM in video #2 of the series by hand cranking it “as fast as he can”, a speed measured by using the metronome app on his smartphone. He begins driving the gearbox with an electric drill in video #3, with some mixed but promising results. We think he will ultimately succeed in his goal of a high-speed, electric-drill-driven gearbox after a few more tests. If you want to have a go at this yourself, the design files are posted online.
How fast do you think he can eventually get this gearbox spinning? Are there any physical limitations of the assembly or due to the 3D printing materials/process? We certainly know that high torque can tear 3D-printed gearboxes apart, but how does the speed affect things? Let us know in the comments below.
Music Box Paper-Punching Machine Settles The Score
As soon as [pashiran] laid eyes on his first hand-cranked music box, he knew he was in love. Then, he started punching the holes for his first ditty. As the repetitive stress of punching heated up his arm, his love cooled a bit. Annealed by the ups and downs of this experience, he decided to design a machine that can punch the holes automatically.
Soon, [pashiran] found his people — a community of music boxers that transform MIDI files to DXF format, which creates coordinates for CAD software. In [pashiran]’s music puncher, an Arduino MEGA takes a DXF file and bubble-sorts the jumble of x-coordinates. The MEGA conducts a trio of two stepper motors and DC motor. One stepper pushes the paper through on the x-axis, and the other moves the puncher head back and forth across the paper scroll as the y-axis. The DC motor moves the punch up and down.
Now, paired with [Martin] of [Wintergatan]’s method for chaining music box paper together, [pashiran] can write a prog-rock-length opus without fear of repetitive stress injury. And since he’s published the STL and INO files, now you can, too. Watch it punch and play 250 notes worth of “See My Vest” “Be Our Guest” after the break.
There’s more than one way to avoid manually punching all those holes. When [Wintergatan] was wrestling this problem, he inspired the hacker community to create a MIDI-to-laser-cut-stencil solution.
Continue reading “Music Box Paper-Punching Machine Settles The Score”
Power Generation Modules Mix And Match Wind, Water, And Hand Cranks
What’s great about the Power Generation Modules project headed by [Cole B] is the focus on usability and modularity. The project is a system for powering and charging small devices using any number and combination of generator modules: wind turbine, hand-crank, and water turbine so far. Power management and storage is handled by a separate unit that acts as a battery bank to store the output from up to six generators at once. There’s also a separate LED lamp module, designed to be capable of being powered directly from any of the generator modules if needed.
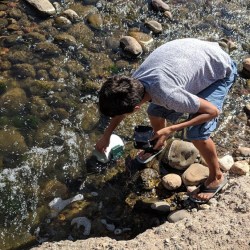
The hand crank is straightforward in concept, but key to usability was selecting a DC gearmotor with a gear ratio that made cranking by hand both comfortable and sustainable; too weak of a crank and it’s awkward, too hard and it’s tiring. The wind turbine has three compact vanes that turn a central shaft, but testing showed the brushless motor it uses as a generator isn’t a good match for the design; the wind turbine won’t turn well in regular wind conditions. The water turbine prototype showed great success; it consists of an epoxy-glazed, 5 inch diameter 3D printed propeller housed in a section of PVC pipe. The propeller drives a brushless motor which [Cole B] says easily outputs between eight to ten volts when testing in a small stream.
The team has plans for other generators such as solar, but this is a great start to an array of modules that can be used to power and charge small devices while off the grid. We’re happy to see them as a finalist for The Hackaday Prize; they were selected as one of the twenty projects to receive $1000 cash each in the Power Harvesting Challenge. The Human-Computer Interface Challenge is currently underway which seeks innovative ideas about how humans and computers can interface with one another, and twenty of those finalists will also receive $1000 each and be in the running for the Grand Prize of $50,000.