We’ve been going on at length in this space about the death spiral that AM radio seems to be in, particularly in the automotive setting. Car makers have begun the process of phasing AM out of their infotainment systems, ostensibly due to its essential incompatibility with the electronics in newer vehicles, especially EVs. That argument always seemed a little specious to us, since the US has an entire bureaucracy dedicated to making sure everyone works and plays well with each other on the electromagnetic spectrum. The effort to drop AM resulted in pushback from US lawmakers, who threatened legislation to ensure every vehicle has the ability to receive AM broadcasts, on the grounds of its utility in a crisis and that we’ve spent billions ensuring that 80% of the population is within range of an AM station.
shipping container7 Articles
Kites Fill Electricity Generation Gaps
Looking at a wind turbine from first principles, it’s essentially a set of wings that generate lift in much the same way an airplane wing does. Putting the wings on a rotor and calling them “blades” is not a huge step away from that. But there’s no reason the wing has to rotate, or for that matter be attached to a fixed platform, in order to generate electricity. Anything that generates lift can be used, and this company is demonstrating that with their kite-powered wind generators.
Like other wind energy producers that have used kites to generate electricity, this one is similar in that the kite is flown in a figure-8 pattern downwind where it can harness energy the most efficiently, pulling out a tether which is tied to a generator. When fully extended, it is flown to a position where the wind doesn’t strike the kite as strongly and the tether is reeled in. Unlike other kite generators we’ve seen, though, this one is offered as a turnkey system complete with battery backup and housed in a self-contained shipping unit, allowing it to be deployed quickly to be used in situations where something like a diesel generator would be impossible to get or where the fuel can’t be obtained.
The company, called Kitepower, does note that these aren’t replacements for traditional wind turbines and would be used more for supporting microgrids. There are still some advantages to using kites over fixed turbine blades though: kites can reach higher altitude where the wind is stronger, and they require less materials for a given amount of energy production, often making them even more environmentally friendly and possibly more economical as well. Surprisingly enough, kites can also be used to generate energy even in places where there’s no wind at all.
Small Swedish Stores Are Miniature Oases In A National Food Desert
It all started one night in 2016 after [Robert Ilijason] dropped the last remaining jar of baby food in the house, breaking it. On the 20-minute drive to the nearest supermarket, he had an idea: what if there were small, 24-hour convenience-level grocery stores that could fill the glaring need for access to basics across the country?
Sweden has lost a few thousand smaller grocery stores in the last 25 years or so, mostly in rural areas. For many people living outside the cities, the nearest place to buy milk is several miles away, at a huge supermarket that’s either in a city, or close to it. After [Robert] built Sweden’s first 24-hour unmanned convenience store, the idea received quite a bit of media attention.
Five years and a pandemic later, the concept is still going strong. A chain of 30 of these bite-sized bodegas have popped up all over Sweden, run by a company called Lifvs. They have no staff at all, not even a cashier. Instead, shoppers unlock the door with their phones. They scan all their barcodes into an app, which provides a bill every month and is linked to both their bank account and national identity system. Beyond that, security is in the form of a single camera.
Because these tiny stores are staff-less, the prices can be kept relatively low. The only problem is that the technology is a bit of an issue for some older residents. Back in 2016, [Robert Ilijason] was trying to figure out another way for customers to unlock the door, but it doesn’t look like Lifvs has solved that problem yet.
One thing you can’t complain about with a store like this is the selection. We have to wonder if shoppers are more or less likely to encounter fasciated fruit amongst the produce.
Field Guide To Shipping Containers
In the 1950s, trucking magnate Malcom McLean changed the world when he got frustrated enough with the speed of trucking and traffic to start a commercial shipping company in order to move goods up and down the eastern seaboard a little faster. Within ten years, containers were standardized, and the first international container ship set sail in 1966. The cargo? Whisky for the U.S. and guns for Europe. What was once a slow and unreliable method of moving all kinds of whatever in barrels, bags, and boxes became a streamlined operation — one that now moves millions of identical containers full of unfathomable miscellany each year.
When I started writing this, there was a container ship stuck in the Suez canal that had been blocking it for days. Just like that, a vital passage became completely clogged, halting the shipping schedule of everything from oil and weapons to ESP8266 boards and high-waist jeans. The incident really highlights the fragility of the whole intermodal system and makes us wonder if anything will change.
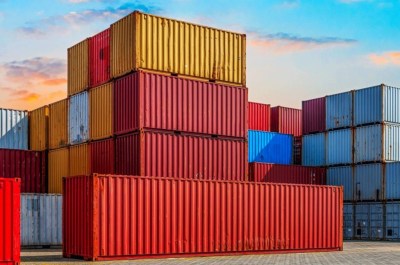
Setting the Standard
We are all used to seeing the standard shipping container that’s either a 10′, 20′, or 40′ long box made of steel or aluminum with doors on one end. These are by far the most common type, and are probably what come to mind whenever shipping containers are mentioned.
These are called dry storage containers, and per ISO container standards, they are all 8′ wide and 8′ 6″ tall. There are also ‘high cube’ containers that are a foot taller, but otherwise share the same dimensions. Many of these containers end up as some type of housing, either as stylish studios, post-disaster survivalist shelters, or construction site offices. As the pandemic wears on, they have become so much in demand that prices have surged in the last few months.
Although Malcom McLean did not invent container shipping, the strict containerization standards that followed in his wake prevent issues during stacking, shipping, and storing, and allow any container to be handled safely at any port in the world, or load onto any rail car with ease. Every bit of the container is standardized, from the dimensions to the way the container’s information is displayed on the end. At most, the difference between any two otherwise identical containers is the number, the paint job, and maybe a few millimeters in one dimension.
Standard as they may be, these containers don’t work for every type of cargo. There are quite a few more types of shipping containers out there that serve different needs. Let’s take a look at some of them, shall we?
The Challenges Of Shipping From China – Life Of A Flailing Tube Man
Last summer was an exercise in developing a completely different kind of product from my normal wheelhouse; a costume. My Halloween costume had been so popular that I decided to have a go at commercializing it, and that took me on a path into manufacturing that I hadn’t yet taken; shipping by boat from China. The short version is it’s a ridiculously difficult mess. Continue reading “The Challenges Of Shipping From China – Life Of A Flailing Tube Man”
Turning A Shipping Container Into A 3D Printer
Built inside a 20-foot shipping container placed on its end, the Kamermaker – ” room maker” in Dutch – is one of the largest 3D printers we’ve ever seen. Able to print objects as big as 2 meter square and 3.5 meters high, the Kamermaker is designed to print huge objects including furniture, architectural elements, and even entire rooms.
The Kamermaker is a collaboration between Architectburo DUS and Utilimaker and the result of wanting to build the world’s largest 3D printer pavilion. Built inside a stainless steel-clad shipping container, the Kamermaker features a scaled-up version of the X, Y, and Z axes you’d find in any other 3D printer. The only change is a scaling up of current designs, allowing it to print small wind turbines covering its surface or, theoretically, a life-size TARDIS.
Because using traditional plastic filament would be prohibitively expensive, the Utilimaker team chose to extrude plastic pellets on the fly as it is used. There’s an excellent video of the filament extruder here along with a walk-through of the machine in operation after the break.
Continue reading “Turning A Shipping Container Into A 3D Printer”
Googles Servers Revealed
We’ve often wondered what kind of hardware the giant of the internet, Google, used to handle it’s data. They’ve recently revealed what their main workhorses are. It’s a custom motherboard made by Gigabyte with two processors, and eight RAM slots. The main point of interest on these is the fact that each server and piece of network equipment has it’s own battery backup. This may add a little money in the initial cost of the unit, but apparently it is a much more efficient way of handling power. Be sure to click over to the site and check out the shipping container setup that they use. Each container has 1,160 servers. They aren’t the only ones using this method. Microsoft has adopted it for their newer facilities and Sun has done some extensive testing on how these portable facilities handle earthquakes. You can see the quake test after the break.