Making lasers smaller and more capable of rapidly alternating between frequencies, while remaining within a narrow band, is an essential part of bringing down the cost of technologies such as LiDAR and optical communication. Much of the challenge here lies understandably in finding the right materials that enable a laser which incorporates all of these properties.
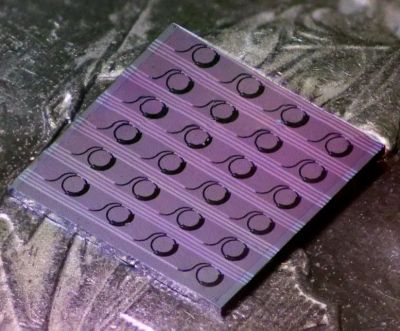
Here a recent study by [Viacheslav Snigirev] and colleagues (press release) demonstrates how combining the properties of lithium niobate (LiNbO3) with those of silicon nitride (Si3N4) into a hybrid (Si3N4)–LiNbO3 wafer stack allows for an InP-based laser source to be modulated in the etched photonic circuitry to achieve the desired output properties.
Much of the modulation stability is achieved through laser self-injection locking via the microresonator structures on the hybrid chip. These provide optical back reflection that forces the laser diode to resonate at a specific frequency, providing the frequency lock. What enables the fast frequency tuning is that this is determined by the applied voltage on the microresonator structure via the formed electrodes.
With a LiDAR demonstration in the paper that uses one of these hybrid circuits it is demonstrated that the direct wafer bonding approach works well, and a number of optimization suggestions are provided. As with all of these studies, they build upon years of previous research as problems are found and solutions suggested and tested. It would seem that thin-film LiNbO3 structures are now finding some very useful applications in photonics.
(Heading image: Stack of Si3N4-LiNbO3 forming the integrated laser and integrated into test setup (d). (Credit: Snigirev et al., 2023) )