In addition to driving home the need for Steadicam or Optical Image Stabilization, this eighty-year-old video illustrates some elegant solutions the automotive industry developed in their suspension systems. Specifically, this Chevrolet video from 1938 is aimed at an audience that values science and therefore the reel boils down the problem at hand using models that will remind you of physics class.
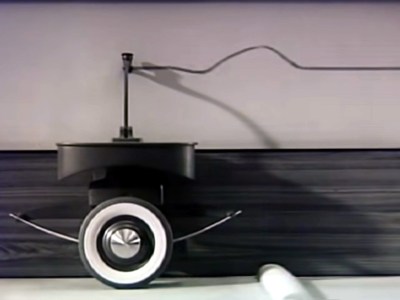
The problem is uneven ground — the “waves in the Earth’s surface” — be it the terrain in an open field, a dirt road, or even a paved parkway. Any vehicle traveling those surfaces will face the challenge of not only cushioning for rough terrain, but accounting for the way a suspension system itself reacts to avoid oscillation and other negative effects. In the video this is boiled down to a 2-dimensional waveform drawn by a model which begins with a single tire and evolves to include a four wheeled vehicle with different suspension systems in the front and the rear.
Perhaps the most illuminating part of the video is the explanation of how the car’s front suspension actually works. The wheels need to be able to steer the vehicle, while the suspension must also allow the tire to remain perpendicular to the roadway. This is shown in the image at the top of this article. Each wheel has a swing arm that allows for steering and for vertical movement of the wheel. A coil spring is used in place of the leaf springs shown in the initial model.
You probably know what’s coming next. The springs are capable of storing and releasing energy, and left to their own devices, they’ll dissipate the energy of a bump by oscillating. This is exactly what we don’t want. The solution is to add shock absorbers which limit how the springs perform. The waveforms drawn by the model encountering bumps are now tightly constrained to the baseline of flat ground.
This is the type of advertising we can wholeheartedly get behind. Product engineers of the world, please try to convince your marketing colleagues to show us the insides, tell us why the choices were made, and share the testing that helps users understand both how the thing works and why it was built that way. The last eighty years have brought myriad layers of complexity to most of the products that surround us, but human nature hasn’t changed; people are still quite curious to see the scientific principles in action all around us.
Make sure you don’t bomb out of the video before the very end. A true bit of showmanship, the desktop model of a car is recreated in a full-sized Chevy, complete with “sky-writing smoke” to draw the line. I don’t think it’s a true analog, but it’s certainly the kind of kitsch I always look for in a great Retrotechtacular subject.
Continue reading “Retrotechtacular: Automotive Suspension Is All About Waves”