In the annals of technical achievement originating from the United Kingdom there lies a forgotten success story that should have led to greater things but instead became a dead-end even before it had happened. We’re referring of course to Prospero, a British satellite that holds the honour of being the only one to have been launched on board a British-developed satellite launch platform. On the 28th of October 1971 it was launched aboard a Black Arrow rocket from the Woomera launch site in Australia and successfully entered orbit to complete its mission. When it was launched the Black Arrow program had already been canceled by the British government, with the launch proceeding only because rocket and satellite were by then already on the pad.
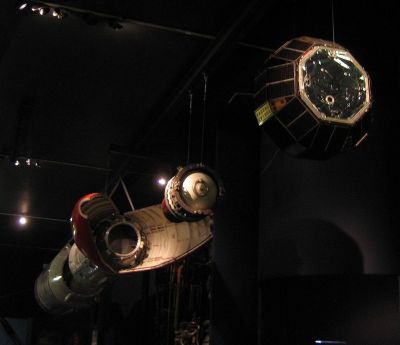
So the Brits became the sixth nation to develop a satellite launch capability, and promptly canned it. Prospero was a success though and remains in orbit, and was even re-activated periodically as late as the 1990s. With its fiftieth anniversary approaching in October we think it’s worth looking for to mark the occasion, and so would like to remind you of its existence and the impending anniversary. If any community can find a lost satellite, hear its call if it is still transmitting anything, and maybe even wake it up, it’s you lot. Hackaday readers never cease to amaze us with their talents, and we know that among you will be people with what it takes to find Prospero.
To help you along your way there’s a lot of information about the satellite to be found online, including the details of an unsuccessful attempt to contact it a decade ago for the anniversary in 2011, and a real-time tracker to help you find its position. Maybe some of you have a decent enough telescope to take a snap of it as it passes over, but if a radio signal could be retrieved from it that would be particularly impressive. Watch out though, you might find yourself hearing an Orbcomm satellite on the same frequency.
So if any of you fancy firing up your SDRs and pointing an antenna skywards over the next few months, we’d like to hear about your progress. It’s possible that the craft may by now be incapable of life, but if anything can be found it’s worth a try.
This isn’t the first satellite rescue attempt documented here on Hackaday. A few years back we put out the call to rescue ICE/ISEE-3.