Traditional airports spend big money to install instrument landing systems (ILS) to guide planes in safely. In places like Antarctica, though, it’s simply not possible to permanently install a massive antenna array for localization, particularly with all the ice shifting about on the regular. As covered by Flightradar24, the solution to this is to use a transponder landing system (TLS) instead.
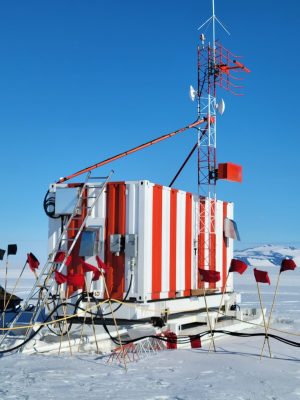
A TLS tracks planes by using multilateration—basically, transponder signals are picked up by multiple antennas and the time delays are used to figure out the position of the aircraft. It then sends the guidance signals a plane would normally expect to receive from an ILS transmitter array, for horizontal and vertical guidance. These signals appear to the plane to be coming from antennas located as per a typical ILS array, with the TLS able to generate signals from ‘virtual emanation points” as needed. This allows the TLS to generate different landing approaches to suit different planes and conditions. From the pilot and aircraft side, it’s all perfectly transparent.
In Antarctica’s McMurdo station, landings are handled by a TLS system that barely takes up more space than a single shipping crate. The system can be set up in just a few hours, unlike a traditional ILS which takes significant installation work spanning weeks or months at best. At the moment, though, the landing strip at McMurdo is stable enough that the system only needs periodic realignment every three years or so.
You might assume that if you’re approaching Antarctica by plane, everything would be on manual. However, the creature comforts of modern airports are available even at one of the the most southerly airports on Earth!