Yesterday, the Indian Space Research Organization’s (ISRO) Chandrayaan-3 spacecraft performed a powered soft-landing on the Moon, officially making India the fourth country to achieve a controlled descent to the lunar surface. Up to this point, only the United States, China, and the Soviet Union could boast successful landings on our nearest celestial neighbor.
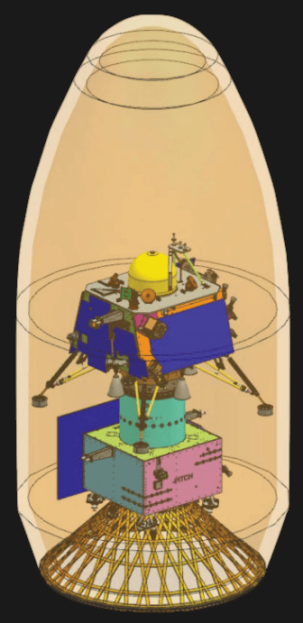
What’s more, Chandrayaan-3 has positioned itself closer to the Moon’s south pole than any other mission in history. This area is of great interest to scientists, as there is evidence that deep craters in the polar region contain considerable deposits of frozen water. At the same time, the polar highlands receive almost constant sunlight, making it the perfect location to install solar arrays. These factors make the Moon’s south pole an ideal candidate for a future human outpost, and Chandrayaan-3 is just one of several robotic craft that will explore this area in the coming years.
But as is usually the case with space exploration, the success of Chandrayaan-3 didn’t come easy, or quickly. The ISRO started the Chandrayaan program in 2003, and launched the Chandrayaan-1 mission in 2008. The craft successfully entered lunar orbit and surveyed the surface using a wide array of instruments, many of which were provided by foreign space agencies such as NASA and the ESA. In 2019 the far more ambitious Chandrayaan-2 mission was launched, which included a lander and small rover. While the orbiter component of Chandrayaan-2 was a complete success, the lander crashed into the Moon’s surface and was destroyed.
With Chandrayaan-3 now safely on the surface of the Moon, there’s much work to be done in the coming days. The planned mission lifetime for both the lander and rover is a single lunar day, which equals just about two weeks here on Earth. After that, the vehicles will be plunged into a long stretch of frigid darkness which they likely won’t survive.
Continue reading “India Makes History With Chandrayaan-3 Landing”