It’s not quite “bend, fold or mutilate” but this project comes close– it actually manufactures a spring clip for [Super Valid Designs] PETAL light system. In the video (embedded below) you’ll see why this tool was needed: by-hand manufacturing worked for the prototype, but really would not scale.
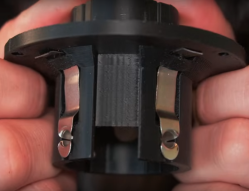
The lights themselves might be worthy of a post, being a modular, open source DMX stage lighting rig. Today though we’re looking at how they are manufactured– specifically how one part is manufactured. With these PETAL lights, the lights slot into a base station, which obviously requires a connection of some sort. [Super Valid Designs] opted for a spring connector, which is super valid.
It’s also a pain to work by hand: spring steel needed to be cut to length, hole punched, and bent into the specific shape required. The hand-made springs always needed adjustment after assembly, too, which is no good when people are giving you money for objects. Even when using a tent-pole spring that comes halfway to meeting their requirements, [Super Valid Designs] was not happy with the workflow. Continue reading “Compound Press Bends, Punches And Cuts Using 3D Printed Plastic”