So far, I’ve talked about why DisplayPort is the future, introduced the basics of how to work with it on the hacker level, took apart and tamed the DisplayPort altmode, and recently, went through the eDP (embedded DisplayPort) display technology. This time, I want to give you a project library to reference, so that your hacking goes as smoothly as possible – real-world examples of open-source DisplayPort boards, a few boards I’ve worked on, part numbers, and whatever other information you might need.
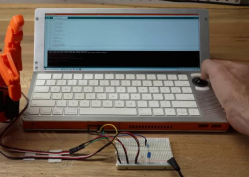
Over the past few years, I’ve noticed that a non-zero amount of cyberdeck builders buy eDP screens with HDMI converter boards on Aliexpress, then connect them to SBCs using USB-C to HDMI adapters, or ignore the onboard eDP port; even this super cool Framework-based cyberdeck has done that! I get that it’s the simplest option, but I do believe that you ought to know how to improve it. The issue is that this double-conversion decreases the battery life significantly by burning two extra ASICs doing video conversion back and forth. Every hour of battery life matters in a cyberdeck, doubly so if it’s based on a low-power device already – you could easily cut your battery life in half if you’re not careful!
With these projects and references in your arsenal, my aim is that DisplayPort becomes way more comfortable for you to work with. Thankfully, there are quite a few projects to reference by now – let’s delve in.
Right out of the gate – are you looking for an SBC with DisplayPort support? The BoardDB website, a database of single-board computers, has a DisplayPort filter – click this link with the filter already enabled and browse through.