BB-8 is the much loved new droid introduced in the 2016 movie Star Wars: The Force Awakens, though in my case from the very first trailer released in 2014 I liked it for the interesting engineering problems it posed. How would you make a robot that’s a ball that rolls along, but with a head that stays on top while the ball rolls under it?
To make the ball roll, the answer most people found obvious at first was to use the analogy of a hamster wheel. The hamster running inside makes the wheel turn. In the BB-8 building world, which is quite large, the drive mechanism has come to be called a hamster drive, or just a hamster.
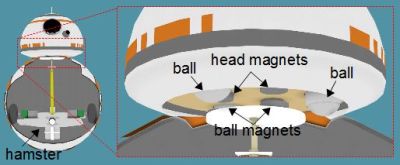
For the head, it seemed obvious that there would be magnets inside the ball, perhaps held in place near the top of the ball by a post extending up from the hamster. Corresponding magnets in attraction would then be attached to the underside of the head, and balls (also mounted under the head) would keep the head moving smoothly over the ball.
The magnet approach for the head has turned out to be the method used by all BB-8 builders that I’ve seen. However, the hamster has turned out to be only one of multiple solutions. Since the original debut many different methods have been used in builds and we’re going to have a lot of fun looking at each separate approach. It’s almost like revealing a magic trick; but really it’s all just clever engineering.
Note that for the actual movie, a combination of 7 or 8 props and CGI were used. The official working BB-8s that are shown at various promotional events were built after the movie was made and as of this writing, few details of their construction have been released. One notable detail, however, is that they aren’t using hamster drives.
Below are details of all the different BB-8 drive systems I’ve seen so far that have been built along with how they work.
Continue reading “Driving BB-8: More Than One Way To Move This Bot”