Looking for ideas for your haptics projects? [Destin] of the Smarter Every Day YouTube channel got a tour from the engineers at HaptX of their full-featured VR glove with amazing haptic feedback both with a very fine, 120-point sense of touch, force feedback for each finger, temperature, and motion tracking.
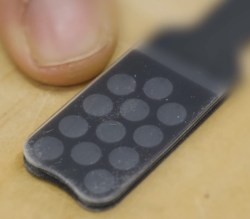
In hacks, we usually stimulate the sense of touch by vibrating something against the skin. With this glove, they use pneumatics to press against the skin. A single fingertip has multiple roughly 1/8 inch air bladders in contact with it. Each bladder is separately pneumatically controlled by pushing air into it. The air pressure can vary continuously so that the bladders can push lightly, harder or anywhere in between. The glove has 120 of these bladders spread out over the fingers and the palm. Unfortunately, they didn’t allow him to see the valves controlling the pneumatics, but if you are looking for a low-frequency, low-cost way to actuate valves you might consider using syringes. The engineers do tell [Destin] that if your VR scene shows something pressing against your virtual finger, as long as your haptics push against your real finger within around 1/8th of a second, your brain won’t notice the delay.
They’re also working on using hot and cold fluids to give a sense of temperature within a glove. This is demonstrated in the first video below when [Destin] feels heat while a dragon in the VR world breathes fire on his hand. Fortunately one of the engineers mentions that our sense of temperature is one of the slower ones, it can handle longer latencies than even touch. We can see implementing this in a hack using a bladder pressing against the skin while tubes circulate different temperature fluids through it. But maybe there’s a way to do it electrically, possibly with thermoelectric modules as is done with this drinks cooler? Though safety issues might prohibit that.
Other features mentioned are force feedback for each finger, and their custom motion tracking which uses both magnetic and optical means to track fingertips. But we’ll leave the rest to the videos below. The first is the technical tour and the second is the glove being used in the VR world.