If you want to build your own rover, there’s plenty of cheap RC trucks out there that will provide a serviceable chassis to work with. Looking to go airborne with a custom drone? Thanks to the immense popularity of first-person view (FPV) flying, you’ll find a nearly infinite variety of affordable fixed wing and quadcopter platforms out there to chose from. But when it comes to robotic watercraft, the turn-key options aren’t nearly as plentiful; the toys are all too small, and the commercial options are priced for entities that have an R&D budget to burn. For amateur aquatic explorers, creativity is the name of the game.
Take for example this impressive vessel built by [wesgood]. With a 3D printed electronics enclosure mounted to a pair of pontoons made of cheap 4-inch PVC pipe available from the hardware store, it provides a stable platform without breaking the bank. Commercial jet drive units built into the printed tail caps for the pipes provide propulsion, and allow the craft to be steered through differential thrust. Without rudders or exposed propellers, this design is particularly well-suited for operating in shallow waters.
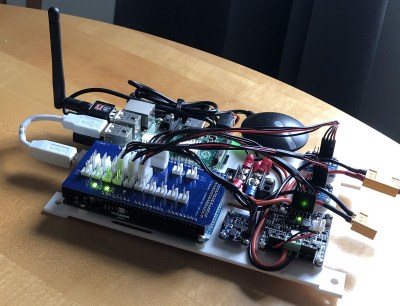
Perched high above the water, the electronics box contains a Raspberry Pi 2, BU353 USB GPS receiver, and a Arduino Mega 2560 paired with a custom PCB that offers up convenient ports to connect a dual-channel Cytron 3 amp motor driver and Adafruit BNO055 9-DOF IMU. Power is provided by two 6,000 mAh LiPo batteries mounted low in the pontoons, and a matching pair of Adafruit current/voltage sensors are used to keep track of the energy budget. A small USB WiFi dongle with an external antenna plugged into the Pi offers up a WiFi network that [wesgood] can connect to with an iPad for control.
If the control software for the craft looks particularly well-polished, it’s probably because [wesgood] just so happens to be a professional developer with a focus on mobile applications. While we’re a bit skeptical of using WiFi for a critical long-distance link, we can’t deny that the iPad allows for a very slick interface. In addition to showing the status of the craft’s various systems, it lets the user either take manual control or place waypoints for autonomous navigation — although it sounds like that last feature is only partially implemented right now.
We love this design, and are eager to see more as the project develops. Recently [wesgood] experimented with payloads that can be suspended from the bottom of the electronics box, specifically a sonar module for performing bathymetric observations. There’s considerable interest in crowd sourced depth maps for inland waterways, and a robotic craft that can reliably chart these areas autonomously is certainly a step up from having to collect the data manually.