There’s just something about a satisfying “click” that our world of touchscreens misses out on; the only thing that might be better than a good solid “click” when you hit a button is if device could “click” back in confirmation. [Craig Shultz] and his crew of fine researchers at the Interactive Display Lab at the University of Illinois seem to agree, because they have come up with an ingenious hack to provide haptic feedback using readily-available parts.
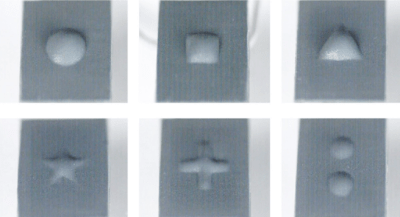
The “hapticoil”, as they call it, has a simple microspeaker at its heart. We didn’t expect a tiny tweeter to have the oomph to produce haptic feedback, and on its own it doesn’t, as finger pressure stops the vibrations easily. The secret behind the hapticoil is to couple the speaker hydraulically to a silicone membrane. In other words, stick the thing in some water, and let that handle the pressure from a smaller soft button on the silicone membrane. That button can be virtually any shape, as seen here.
Aside from the somewhat sophisticated electronics that allow the speaker coil to be both button and actuator (by measuring inductance changes when pressure is applied, while simultaneously driven as a speaker), there’s nothing here a hacker couldn’t very easily replicate: a microspeaker, a 3D printed enclosure, and a silicone membrane that serves as the face of the haptic “soft button”. That’s not to say we aren’t given enough info replicate the electronics; the researchers are kind enough to provide a circuit diagram in figure eight of their paper.
In the video below, you can see a finger-mounted version used to let a user feel pressing a button in virtual reality, which raises some intriguing possibilities. The technology is also demonstrated on a pen stylus and a remote control.
This isn’t the first time we’ve featured hydraulic haptics — [Craig] was also involved with an electroosmotic screen we covered previously, as well as a glove that used the same trick. This new microspeaker technique does seem much more accessible to the hacker set, however.
Continue reading “Haptic Soft Buttons Speak(er) To Your Sense Of Touch”