After World War II, as early supersonic military aircraft were pushing the boundaries of flight, it seemed like a foregone conclusion that commercial aircraft would eventually fly faster than sound as the technology became better understood and more affordable. Indeed, by the 1960s the United States, Britain, France, and the Soviet Union all had plans to develop commercial transport aircraft capable flight beyond Mach 1 in various stages of development.
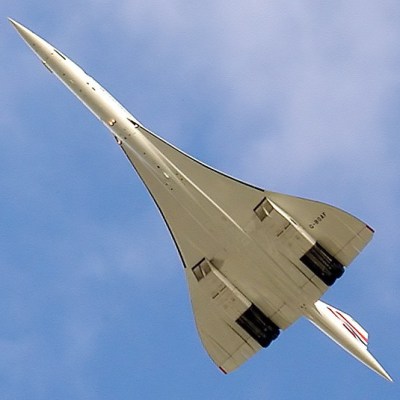
Yet today, the few examples of supersonic transport (SST) planes that actually ended up being built are in museums, and flight above Mach 1 is essentially the sole domain of the military. There’s an argument to be made that it’s one of the few areas of technological advancement where the state-of-the-art not only stopped moving forward, but actually slid backwards.
But that might finally be changing, at least in the United States. Both NASA and the private sector have been working towards a new generation of supersonic aircraft that address the key issues that plagued their predecessors, and a recent push by the White House aims to undo the regulatory roadblocks that have been on the books for more than fifty years.
Continue reading “Supersonic Flight May Finally Return To US Skies”