3D scanning is becoming much more accessible, which means it’s more likely that the average hacker will use it to solve problems — possibly odd ones. That being the case, a handy tool to have in one’s repertoire is a way to work with point clouds. We’ll explain why in a moment, but that’s where CloudCompare comes in (GitHub).
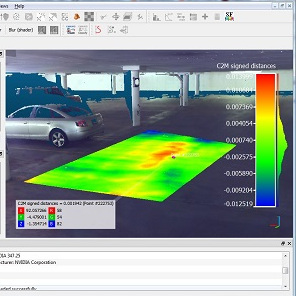
CloudCompare is an open source tool with which one can load up and do various operations on point clouds, including generating mesh models from them. Point clouds are what 3D scanners create when an object is scanned, and to become useful, those point clouds are usually post-processed into 3D models (specifically, meshes) like an .obj
or .stl
file.
We’ve gone into detail in the past about how 3D scanning works, what to expect from it, and taken a hands-on tour of what an all-in-one wireless scanner can do. But what do point clouds have to do with getting the most out of 3D scanning? Well, if one starts to push the boundaries of how and to what purposes 3D scanning can be applied, it sometimes makes more sense to work with point clouds directly instead of the generated meshes, and CloudCompare is an open-source tool for doing exactly that.
For example, one may wish to align and merge two or more different clouds, such as from two different (possibly incomplete) scans. Or, you might want to conduct a deviation analysis of how those different scans have changed. Alternately, if one is into designing wearable items, it can be invaluable to be able to align something to a 3D scan of a body part.
It’s a versatile tool with numerous tutorials, so if you find yourself into 3D scanning but yearning for more flexibility than you can get by working with the mesh models — or want an alternative to modeling-focused software like Blender — maybe it’s time to work with the point clouds directly.