Most of us have seen those demonstrations of metal parts that mate together so finely that, once together, they have no visible seam at all. But how, exactly, is this done? [Steve Mould] has a video that shows and explains all, and we’ve never seen the process explained quite like he does.
The secret ingredient is wire EDM, or Electrical Discharge Machining, but that’s only one part of the whole. Wire EDM works a bit like a hot-wire cutter slicing through foam, but all by itself that’s not enough to produce those impossibly close-fitting parts we love to see.
EDM is capable of astounding precision in part because — unlike a cutting tool — nothing physically contacts the material. Also, there isn’t a lot of friction and heat causing small distortions of the material during the machining process. EDM is as a result capable of fantastically-precise cuts, but not invisible ones.
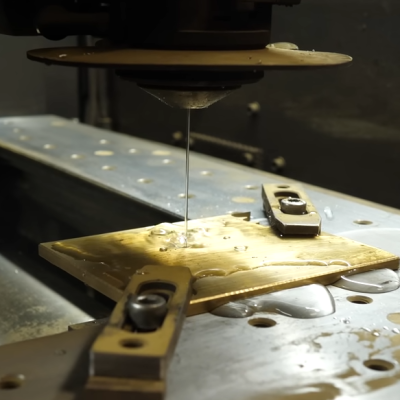
In all good manufacturing, the capabilities (and limitations) of the tool are taken into account, and this is also true for making those close-fitting pieces. The hole and plug are actually made in two separate stages.
The hole is cut separately from the plug, and because EDM is capable of such finesse, the cuts can be made in such a way that they complement one another with near-perfection. After that, grinding and polishing takes care of the surface finish. The result is the fantastically-smooth and apparently seamless fitment we like so much.
The video is embedded below, and there are some great details about EDM and how it actually works in there. For example, we see how a wire EDM machine can use a jet of water to help thread the wire through a hole in the part to start a job, and we learn that the wire is constantly moving during the process.
As cool as wire EDM is, it is not magic and we’ve seen some pretty remarkable efforts at bringing the technology into the home workshop.
Continue reading “Learn How Impossibly Close-fitting Parts Are Actually Made”