[Cyrill] has a good home automation scheme going: there are a number of physical switches set around the place that control the essential functions. The only problem is that in the winter time, this results in a great deal of phone checking as [Cyrill] tries to monitor the CO2 level. Tired of all this screen time, [Cyrill] set about to create an incredibly cute (and useful) Co2 monitor that plainly shows the current level and how bad it is, relatively speaking.
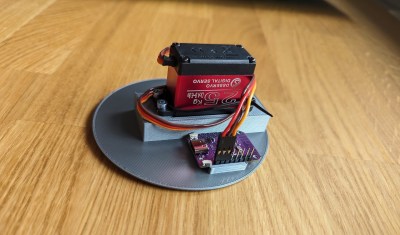
Behind that adorable face is a DS3225 servo being driven by a Wemos S2 mini, both of which [Cyrill] happened to have handy. Although the 25 Kg servo may be complete overkill for the situation, [Cyrill] reports that it is quieter than your average AliExpress alternatives, which makes it well worth it in our book. Then it was on to Inkscape to make the gauge itself. [Cyrill] says they’re an Inkscape noob, but that face could have fooled us.
Finally, it was time to integrate it into Home Assistant to get readings from the CO2 sensors. This was easier said than done, but [Cyrill] does a nice job of explaining how to get the ESP32-S2 up and working.
If you’re out there monitoring CO levels in your home, beware of fake sensors that cropped up during the height of the pandemic and are likely still at large.