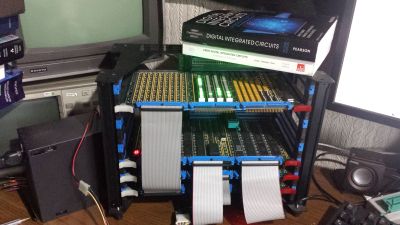
While the concept of a computer system implemented in discrete logic ICs is by itself not among the most original ideas, the way some machines are executed certainly makes them stick out. This is the case with [Paulo Constantino]’s Sol-1, which not only looks extremely professional, but also comes with a lot of amenities that allow for system development, including a C compiler and assembler, a Unix-like OS (in development), DMA, and a whole host of interfaces to interact with the system and peripherals (serial, parallel, IDE, etc.). Not to mention a SystemVerilog model and an emulator, all of which can be found on [Paulo]’s GitHub.
More photos and videos can be found on [Paulo]’s YouTube channel, as well as the Sol-1 website, which shows off the intricate wire wrap work on the back of each PCB. In terms of the ISA, there are 5 general purpose registers (one scratch) which can also be used as two 8-bit registers each. Most operations are supported, except for floating point. For future improvements and additions, Sol-1’s OS will get more features added, and the first major software to be ported to the Sol-1 should be Colossal Cave Adventure and similar text-based adventure (dungeon) games.