This year’s Hackaday Prize is our first nice round number – number ten! We thought it would be great to look back on the history of the Prize and cherry-pick our favorite themes from the past. Last year’s entire theme was sustainable hacking, and we challenged you to come up with ways to generate or save power, keep existing gear out of the landfill, find clever ways to encourage recycling or build devices to monitor the environment and keep communities safer during weather disasters, and you all came through. Now we’re asking you to do it again.
There are hundreds of ways that we can all go a little bit lighter on this planet, and our Green Hacks Challenge encourages you to make them real. Whether you want to focus on clean energy, smarter recycling, preventing waste, or even cleaning up the messes that we leave behind, every drop of oil left unburned or gadget kept out of the landfill helps keep our world running a little cleaner. Here’s your chance to hack for the planet.
Inspiration
One thing we really loved about last year’s Green Hacks was that it encouraged people to think outside the box. For instance, we got some solar power projects as you’d expect, but we also got a few really interesting wind power entries, ranging from the superbly polished 3D Printed Portable Wind Turbine that won the Grand Prize to the experimental kite turbine in Energy Independence While Travelling, to say nothing of the offbeat research project toward making a Moss Microbial Fuel Cell.
3D Printed Portable Wind Turbine
Moss Microbial Fuel Cell
Energy Independence While Travelling
Plastic was also in the air last year, as we saw a number of projects to reuse and recycle this abundant element of our waste stream. From a Plastic Scanner that uses simple spectroscopy to determine what type of plastic you’re looking at, to filament recyclers and trash-based 3D printers to make use of shredded plastic chips.
Polyformer
The Trash Printer – Version 3
Plastic Scanner
Finally, you all really put the science into citizen science with projects like OpenDendrometer that helps monitor a single tree’s health, and the Crop Water Stress Sensor that does the same for a whole field. Bees didn’t get left out of the data collection party either, with the Beehive Monitoring and Tracking project. And [Andrew Thaler]’s tremendously practical Ocean Sensing for Everyone: The OpenCTD brought the basics of oceanic environmental monitoring down to an affordable level.
OpenDendrometer
Crop Water Stress Sensor
Beehive Monitoring and Tracking
Ocean Sensing for Everyone: The OpenCTD
Now It’s Your Turn to be Green
If any of the above resonates with your project goals, it’s time to put them into action! Start up a new project over on Hackaday.io, enter it into the Prize, and you’re on your way. Ten finalists will receive $500 and be eligible to win the Grand Prizes ranging from $5,000 to $50,000. But you’ve only got until Tuesday, July 4th to enter, so don’t sleep.
As always, we’d like to thank our sponsors in the Hackaday Prize, Supplyframe and DigiKey, but we’d also like to thank Protolabs for sponsoring the Green Hacks challenge specifically, and for donating a $5,000 manufacturing grant for one finalist. Maybe that could be you?
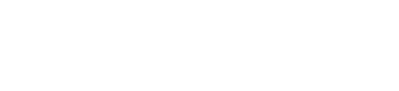