There are many applications for particle accelerators, even outside research facilities, but for the longest time they have been large, cumbersome machines, not to mention very expensive to operate. Here laser wakefield accelerators (LWFAs) are a promising alternative, which uses lasers to create accelerated particles along the wake in a plasma field. One of the major struggles has been with reinjecting the thus accelerated particles into another stage of a multi-stage accelerator, which would be required to obtain energies closer to one TeV. In this area researchers have now demonstrated a way around this, by using curved channels for the laser beams (paywalled paper) which inject the laser beam into the continuous cavity. Continue reading “Accelerating Electrons To TeV Levels Using Curved Laser Beams”
“Room Temperature Superconductor” LK-99, Just Maybe It Could Be Real
To have been alive over the last five decades is to have seen superconductors progress from only possible at near-absolute-zero temperatures, to around the temperature of liquid nitrogen in the 1980s and ’90s, and inching slowly higher as ever more exotic substances are made and subjected to demanding conditions. Now there’s a new kid on the block with an astounding claim of room-temperature and pressure superconductivity, something that has been a Holy Grail for physicists over many years.
LK-99 is a lead-copper-phosphate compound developed by a team from Korea University in Seoul. Its announcement was met with skepticism from the scientific community and the first attempts to replicate it proved unsuccessful, but now a team at Huazhong University of Science and Technology in China claim to have also made LK-99 samples that levitate under a magnetic field at room temperature and pressure. This is corroborated by simulation studies that back up the Korean assertions about the crystal structure of LK-99, so maybe, just maybe, room temperature and pressure superconductors might at last be with us.
Floating on a magnetic field is cool as anything, but what are the benefits of such a material? By removing electrical resistance and noise from the equation they hold the promise of lossless power generation and conversion along with higher-performance electronics both analogue and digital, which would revolutionize what we have come to expect from electronics. Of course we’re excited about them and we think you should be too, but perhaps we’ll wait for more labs to verify LK-99 before we celebrate too much. After all, if it proves over-optimistic, it wouldn’t be the first time.
All American Five Lives Again
If you haven’t heard of an “all-American five,” then you probably don’t dig through bins for old radios. The AA5 is a common design for old AM radios that use five tubes: a rectifier, an oscillator/mixer, an IF amplifier, a detector, and a single tube for driving the speaker. [Mikrowave1] took an old specimen of such a radio from the mid-1950s and wanted to restore it. You can see how it went in the video below.
One feature of the design is that the set had a “hot chassis,” which means you really want to use an isolation transformer before you work on it. We were taught to touch a chassis with the back of our hand first because of radios like this. If it is “hot,” the muscle contraction would throw your arm away from the radio instead of forcing you to grip it uncontrollably.
The GE radio had many quality design touches you don’t always see in a radio like this. The mix of brands indicates that the radio has had tubes replaced in the past. It also had a clearly replaced electrolytic capacitor. Surprisingly, all the tubes were good, although the power output tube was marginal. However, a light bulb was bad and required a little surgery to allow for a slightly different replacement.
Some capacitors were neatly replaced, also. A lot of cleaning and testing later — along with a dropped tool — the radio was ready to play again. Fixing radios from this era is a great hobby. You can get to everything and you don’t really need anything fancy, although a tube tester is helpful. The classic method of troubleshooting is to either find audio on the volume control or not and then work your way backward or forward using a signal tracer or — since they are so readily available now — a scope. Alternatively, you could inject a signal at the volume control and work your way through the circuit until you can or can’t hear the injected signal.
Not the first tube radio we’ve watched being restored, of course. Need a tube tester?
Making Your Own VR Headset? Consider This DIY Lens Design
Lenses are a necessary part of any head-mounted display, but unfortunately, they aren’t always easy to source. Taking them out of an existing headset is one option, but one may wish for a more customized approach, and that’s where [WalkerDev]’s homebrewed “pancake” lenses might come in handy.
Engineering is all about trade-offs, and that’s especially true in VR headset design. Pancake lenses are compact units that rely on polarization to bounce light around internally, resulting in a very compact assembly at the cost of relatively poor light efficiency. That compactness is what [WalkerDev] found attractive, and in the process discovered that stacking two different Fresnel lenses and putting them in a 3D printed housing yielded a very compact pancake-like unit that gave encouraging results.
This project is still in development, and while the original lens assembly is detailed in this build log, there are some potential improvements to be made, so stay tuned if you’re interested in using this design. A DIY headset doesn’t mean you also must DIY the lenses entirely from scratch, and this option seems economical enough to warrant following up.
Want to experiment with mixing and matching optics on your own? Not only has [WalkerDev]’s project shown that off-the-shelf Fresnel lenses can be put to use, it’s in a way good news that phone-based VR is dead. Google shipped over 10 million cardboard headsets and Gear VR sold over 5 million units, which means there are a whole lot of lenses in empty headsets laying around, waiting to be harvested and repurposed.
The Past, Present, And Future Of CircuitPython
Modern microcontrollers like the RP2040 and ESP32 are truly a marvels of engineering. For literal pocket change you can get a chip that’s got a multi-core processor running at hundreds of megahertz, plenty of RAM, and more often than not, some form of wireless connectivity. Their capabilities have been nothing short of revolutionary for the DIY crowd — on any given day, you can see projects on these pages which simply wouldn’t have been possible back when the 8-bit Arduino was all most folks had access to.
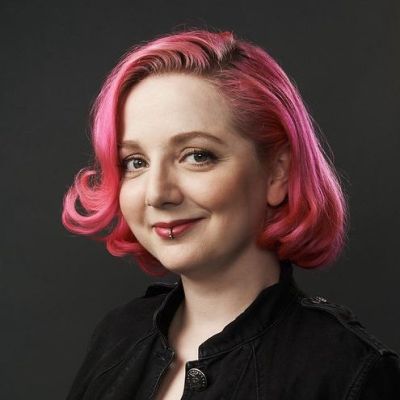
Thanks to the increased performance of these MCUs, hackers and makers now even have a choice as to which programming language they want to use. While C is still the language of choice for processor-intensive tasks, for many applications, Python is now a viable option on a wide range of hardware.
This provides a far less intimidating experience for newcomers, not just because the language is more forgiving, but because it does away with the traditional compile-flash-pray workflow. Of course, that doesn’t mean the more experienced MCU wranglers aren’t invited to the party; they might just have to broaden their horizons a bit.
To learn more about this interesting paradigm shift, we invited the fine folks at Adafruit to the Hack Chat so the community could get a chance to ask questions about CircuitPython, their in-house Python variant which today runs on more than 400 devices.
Continue reading “The Past, Present, And Future Of CircuitPython”
Examining Test Gear From Behind The Iron Curtain
Back in 1978, an oscilloscope was an exotic piece of gear for most homebrewers. We expect they were even more rare in private hands behind the iron curtain, and [Thomas Scherrer] shows us a Soviet X1-7B combination oscilloscope and spectrum analyzer (he thinks, at least, it is a spectrum analyzer) that he got working.
The Soviet scope is clearly different with its Cyrillic front panel. Luckily, Google Translate was up to the task of decoding a picture of the device. However, the differences aren’t just cosmetic. The scope also has a very interesting rotating bezel around the round CRT. You can see a video of the 8.2 kg scope below.
A quick look inside looks pretty conventional for a scope of that era that used all transistors in the circuitry. The rotating bezel, though, also controls something that looks like a big mechanical switch and cavity or, perhaps, a big mechanical variable component of some kind.
Satisfied that the insides were in reasonable shape, [Thomas] was ready to try turning it on. We want to say it went well, but… there was censored audio, along with a loud noise, right after it was plugged in. Troubleshooting centered on what was producing a burned smell, but a quick examination didn’t turn up anything obvious, despite being localized to the power circuitry. The fuse didn’t blow, oddly, and — even more puzzling — the unit was off when plugged in!
It turns out the input power filter leaked to the chassis. Since he had a ground on the chassis, that explained the failure, and while it was annoying, it was better than getting a shock with a hot chassis. The second plug in went better.
It finally did work, at least somewhat, although he never explored some of the odd features the scope appears to have. We love the old boat anchor scopes but don’t see many Soviet instruments, at least not those of us on this side of the Atlantic.
We do see a few Soviet-era computers now and again. As for the fuse not blowing, it was shorted before the fuse, but apparently, fuses don’t always blow when you expect them to, anyway.
Continue reading “Examining Test Gear From Behind The Iron Curtain”
Jenny’s Daily Drivers: FreeBSD 13.2
Last month I started a series in which I try out different operating systems with the aim of using them for my everyday work, and my pick was Slackware 15, the latest version of the first Linux distro I tried back in the mid 1990s. I’ll be back with more Linux-based operating systems in due course, but the whole point of this series is to roam as far and wide as possible and try every reasonable OS I can. Thus today I’m making the obvious first sideways step and trying a BSD-based operating system. These are uncharted waters for me and there was a substantial choice to be made as to which one, so after reading around the subject I settled on FreeBSD as it seemed the most accessible.
First, A Bit Of Context
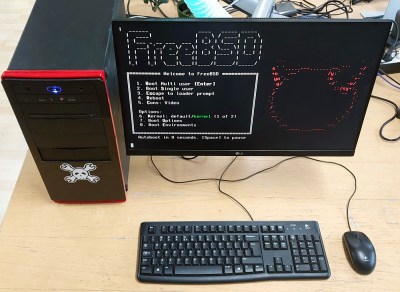
Most readers will be aware that the BSD operating systems trace their heritage in a direct line back to the original AT&T UNIX, while GNU/Linux is a pretty good UNIX clone originating with Linus Torvalds in the early 1990s and Richard Stallman’s GNU project from the 1980s onwards. This means that for Linux users there’s a difference in language to get used to.
Where Linux is a kernel around which distributions are built with different implementations of the userland components, the various BSD operating systems are different operating systems in their own right. Thus we talk about for example Slackware and Debian as different Linux distributions, but by contrast NetBSD and FreeBSD are different operating systems even if they have a shared history. There are BSD distributions such as GhostBSD which use FreeBSD as its core, but it’s a far less common word in this context. So I snagged the FreeBSD 13.2 USB stick file from the torrent, and wrote it to a USB Flash drive. Out with the Hackaday test PC, and on with the show. Continue reading “Jenny’s Daily Drivers: FreeBSD 13.2”