It should come as no surprise that the COVID-19 pandemic has sparked renewed interest in robotic deliveries. Amazon saying they would some day land Prime orders in your backyard with a drone sounded pretty fanciful a few years ago, but now that traditional delivery services are under enormous strain and people are looking to avoid as much human contact as possible, it’s starting to make a lot more sense.
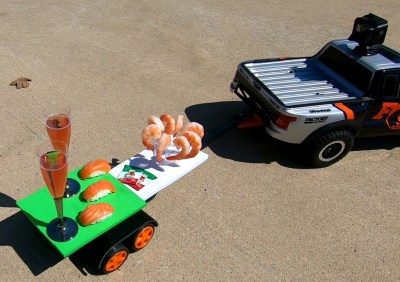
Now to be clear, we don’t think you’ll be seeing this modified RC truck rolling up your driveway with a pizza in tow anytime soon. But the experiments that [Sean] has been doing with it are certainly interesting, and show just how far autonomous rover technology has progressed at the hobbyist level. Whether you need to move some sushi or a sensor package, his build is a great starting point for anyone interested in DIY robotic ground vehicles.
Especially if you want to take things off the beaten path once and awhile. By combining the Pixhawk autopilot system with an off-road RC truck by Traxxas, [Sean] has created a delivery bot that’s not afraid of a little mud. Or even the occasional jump, should the need arise. Just don’t expect your shrimp cocktail and champagne to arrive in one piece after they’ve been given the Dukes of Hazzard treatment.
In the video after the break [Sean] goes over some of the lessons learned on this build, including how he managed to keep the electronics from cooking themselves in the Texas heat. He also goes over the realities of building an autonomous driving system that doesn’t actually have a camera onboard; sure you can plan a route for it in advance, but all bets are off if an unexpected obstacle blocks the path. It’s a pretty serious shortcoming he’s looking to address in the future, as well as upgrading to a far more accurate RTK-GPS receiver.
Continue reading “Autonomous Off-Road Food Delivery With Pixhawk”