In August 2000, Tiger Electronics released HitClips: Music cartridges and players designed to easily share 60 second low quality Clips of a youngster’s favorite Hits. Various players were available, and individual cartridges were inexpensive enough to collect. And it’s these toy music players that [Guy Dupont] has been hacking quite successfully on as you can see in the video after the break and on [Guy]’s Hackaday.io page.
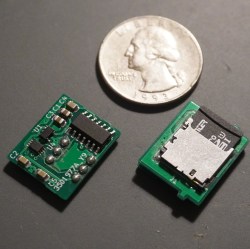
[Guy]’s main goal was to make cartridges of his own that could not just hold more music than the short clips in the commercially made product, but could make use of modern technology that has matured since HitClips came onto the scene more than 20 years go.
The project’s components are relatively simple, but beautifully executed. An ATTINY84 didn’t work out, so a SAM D09 controller was put it place to to read files from a microSD card and translate the WAV file into the HitClips player’s format. 3d printed cartridges and custom PCB’s complete the hack, ensuring that you can use any of the many HitClips players to play something new for a change.
The end result is quite good, considering that it’s still just 8 bit audio on a 20 year old toy player. Tiger Electronics made another toy that’s quite popular with hackers of the musical kind.
Continue reading “HitClips Custom Cartridge Hack Will Never Give Up, Let Down, Or Turn Around”