Quadcopter type drones can be flown indoors, but unless you have a lot of space, it usually just ends in a crash. The prospect of being hit in the face by the propellor blades, spinning at 10k RPM doesn’t bear thinking about, and then there’s the noise. So, as a solution for indoor photography, or operating in public spaces, they are not viable. Japanese mobile operator DOCOMO has a new take on an old idea; the blimp. But, surely even a helium filled vehicle needs blades to steer around the room, we hear you cry? Not so, if you use a pair of specialised ultrasonic transducer arrays to move the air instead! (Video, embedded below)
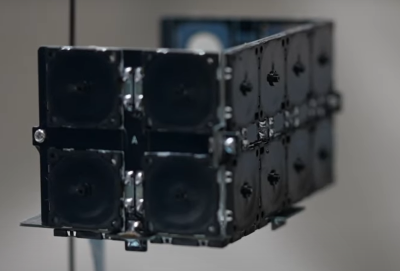
Details are scarce, but DOCOMO have fitted a helium balloon with modules on either side that can produce a steerable thrust, allowing the vehicle to effect all the expected aerial manoeuvres with ease and grace. The module at the bottom contains the control electronics, an upwards facing RGB LED for some extra bling, and of course a video camera to capture those all-important video shots.
We’d love to find a source for those ultrasonic transducer devices, and can only guess at the physical arrangement that allows for air to pass in one direction only, to effect a net thrust. We can find a few research papers hinting at the ability to use ultrasound to propel through air, like this one (bah! IEEExplore Paywall!) but to our knowledge, this technology is not quite in the hands of hackers just yet.
Blimps are by no means scarce on these fine pages, here is a Blimpduino, an Arduino controlled 3D printed blimp, an illuminated blimp art installation by Japanese artist [Kensho Miyoshi] and if using helium is just too darn safe for you (or if you want to help prevent this allegedly precious resource from being lost into space) you could just build a remote controlled blimp using hydrogen instead. Just don’t light a match.
Continue reading “Indoor Blimp Sails Through The Air Using Ultrasonic Transducers”