Whether you’re a landlubber or an old salt, you’ve got to appreciate the effort that [The Aussie boat guy] puts into cutting an old brass propeller down into a far smaller and sleeker specimen. Especially since he does the entire thing with hand tools, a couple different calipers, and that most valuable of natural resources: experience.
The whole process was made somewhat easier by the fact that [The Aussie boat guy] had a model to work from — his friend had a small propeller that was already known to perform well, it was just a matter of cutting the larger prop down to match its dimensions. Using what appears to be pieces of leather (presumably for its flexibility), a template was made to accurately map out the front face of the blade.
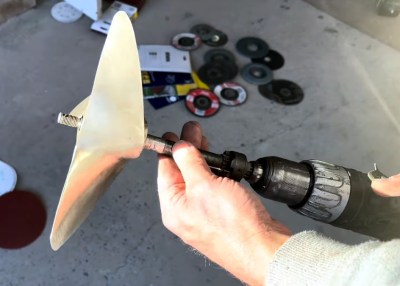
By measuring out from the hub of the prop with his calipers, [The Aussie boat guy] was able to make sure the template was properly positioned before scribing its shape into the larger prop. An angle grinder was used to cut the shape out of each blade, followed by a smoothing off with a flap wheel.
But there was still a problem — the blades were the right shape, but they were far too thick. So he took the angle grinder to the back of each one to start removing material, using another set of calipers to occasionally spot-check them to make sure they were thinning out at roughly the same rate.
This thinning out process continued until the prop was brought into balance. How do you check that, you might be wondering? Well, if you’re a madman like [The Aussie boat guy], you chuck the thing into a power drill and spin er’ up to see how badly it shakes. But this only gives you a rough idea, so he has to move over to a somewhat more scientific apparatus that uses a set of parallel bars to help determine which blade is heavier than its peers.
Continue reading “Brass Propeller Gets Impressive Hand Trimming”