On today’s episode of ‘this is a really neat video that will soon be demonetized by YouTube’ comes this fantastic build from [John]. It is the Golden Gun, or at least it looks like a Golden Gun because it’s made out of melted down brass casings. It’s a masterclass demonstration of melting stuff down and turning a thirteen-pound blob of metal into a two-pound precision machined instrument.
This build began by simply cutting a wooden block, packing it in sand, and melting approximately 1425 shell casings of various calibers in a DIY furnace. The molten brass was then simply poured into the open mold. This is standard yellow brass, with about 70% copper and 30% zinc. There’s a bit of aluminum in there from the primers, and the resulting block isn’t terribly great for machining. [John] says this could be fixed by adding a few percent of lead to the melt. To all the jokesters suggesting he add some unfired bullets to the melt, don’t worry, we already have that covered.
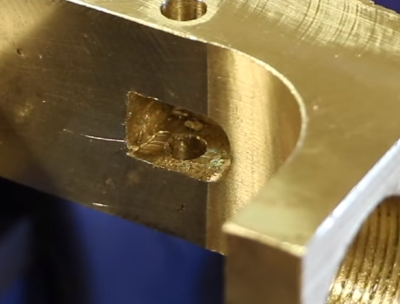
The machining went as you would expect it would with a large mill, but there are a few things that made this entire video worthwhile. For some of the holes, [John] had to square up the corners. The simplest and easiest way to do this is to break out a file. This is brass, though, and with some steel chisels hanging around the shop your mortise and tenon skills might come in handy. With the very careful application of force, [John] managed to put corners on a circle with a standard wood chisel. A bit later in the build video, a few more sharp corners were created by shoving a broach in the mill and jamming it down into the work.
When it comes to machining builds, this is high art. Yes, it’s the same as building an AR-15 out of a few hundred soda cans, but this one is made out of brass. It looks just great, and that final polish turns the entire project into something that looks like it’s out of a video game. Simply amazing.
If you’re looking for more ways to push your metalwork boundaries, give cast iron a try!
Continue reading “Is It A Golden Gun If It’s Made Out Of Brass?”