I was reading Sonya Vasquez’s marvelous piece on the capstan equation this week. It’s a short, practical introduction to a single equation that, unless you’re doing something very strange, covers everything you need to know about friction when designing something with a rope or a cable that has to turn a corner or navigate a wiggle. Think of a bike cable or, in Sonya’s case, a moveable dragon-head Chomper. Turns out, there’s math for that! Continue reading “Run The Math, Or Try It Out?”
engineering83 Articles
Cable Mechanism Maths: Designing Against The Capstan Equation
I fell in love with cable driven mechanisms a few years ago and put together some of my first mechanical tentacles to celebrate. But only after playing with them did I start to understand the principles that made them work. Today I want to share one of the most important equations to keep in mind when designing any device that involves cables, the capstan equation. Let some caffeine kick in and stick with me over the next few minutes to get a sense of how it works, how it affects the overall friction in your system, and how you can put it to work for you in special cases.
A Quick Refresher: Push-Pull Cable Driven Mechanisms
But first: just what exactly are cable driven mechanisms? It turns out that this term refers to a huge class of mechanisms, so we’ll limit our scope just to push-pull cable actuation systems.
These are devices where cables are used as actuators. By sending these cables through a flexible conduit, they serve a similar function to the tendons in our body that actuate our fingers. When designing these, we generally assume that the cables are both flexible and do not stretch when put in tension. Continue reading “Cable Mechanism Maths: Designing Against The Capstan Equation”
Kipp Bradford Discusses The Entanglement Of Politics And Technology
Kipp Bradford wrapped up his keynote talk at the Hackaday Remoticon with a small piece of advice: don’t built bridges in the middle of the ocean. The point is that a bridge must connect two pieces of land to be useful and if technology isn’t useful to humanity, does it matter at all?
In reality we build bridges in the middle of the ocean all the time as each of us finds nonsensical reasons to learn new skills and try things out. But when it comes time to sit down and make an organized end goal, Kipp wisely asks us to consider the impact we’d like that work to have on the world. Equally importantly, how will we make sure completed work actually gets used? This is where the idea of politics in technology comes to play, in the sense that politics is a major mechanism for collective decision-making within a society.
Currently the CTO of Treau, and a Lecturer and Researcher at Yale, Kipp delivered this keynote live on November 7th. Kipp was an expert judge for the Hackaday Prize in 2017 and 2018. The video of his talk, and a deeper look at the topics, are found below.
Continue reading “Kipp Bradford Discusses The Entanglement Of Politics And Technology”
Cardboard Models Trace Design Process Of Vintage Tektronix Miniscopes
There aren’t many brands that inspire the kind of passion and fervency among its customers as Tektronix does. The venerable Oregon-based manufacturer of top-end test equipment has produced more collectible gear over the last 75 years than just about anyone else.
Over that time they have had plenty of innovations, and in the 1970s they started looking into miniaturizing their flagship oscilloscopes. The vintageTEK museum, run by current and former employees, has a review of the design process of the 200 series of portable oscilloscopes that’s really interesting. At a time when scopes were portable in the way a packed suitcase is portable, making a useful instrument in a pocketable form factor was quite a challenge — even for big pockets.
The article goes into great detail on the back-and-forth between the industrial designers, with their endless stream of models, and the engineers who would actually have to stuff a working scope into whatever case they came up with. The models from the museum’s collection are wonderful bits of history and show where the industrial designers really pushed for some innovative designs.
Some of the models are clearly derived from the design of the big bench scopes, but some have innovative flip-down covers and other interesting elements that never made it to production. Most of the models are cardboard, but some were made of aluminum in the machine shop and sport the familiar “Tek blue” livery. But the pièce de résistance of the collection is a working engineering model of what would become the 200-series of miniscopes, a handmade prototype with a tiny round CRT and crudely labeled controls.
The vintageTEK museum sounds like another bucket-list stop for computer and technology history buffs. Tek has been doing things their own way for a long time, and stopping by the museum is sure to be a treat.
Thanks to [Tanner Bass] for the tip.
The Prusa I3 MK3S And A Tale Of Two Sensors
When the Prusa i3 MK3 was released in 2017, it was marketed as being “bloody smart” thanks to the impressive number of sensors that had been packed into the printer. The update wasn’t really about improving print quality over the MK2, but rather to make the machine easier to use and more reliable. There was a system for resuming prints that had stopped during a power outage, a thermometer so the firmware could compensate against thermal drift in the inductive bed sensor, RPM detection on all of the cooling fans, and advanced Trinamic stepper drivers that could detect when the printer had slipped or gotten stuck.
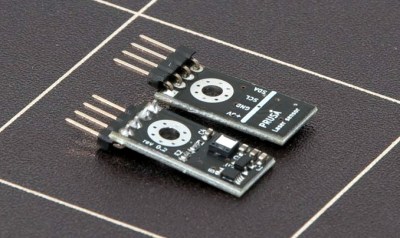
But the most exciting upgrade of all was the new filament sensor. Using an optical encoder similar to what you’d find in a mouse, the Prusa i3 MK3 could detect when filament had been inserted into the extruder. This allowed the firmware to pause the print if the filament had run out, a feature that before this point was largely unheard of on consumer-grade desktop 3D printers. More than that, the optical encoder could also detect whether or not the filament was actually moving through the extruder.
In theory, this meant the MK3 could sense problems such as a jammed extruder or a tangle in the filament path that was keeping the spool from unrolling. Any other consumer 3D printer on the market would simply continue merrily along, not realizing that it wasn’t actually extruding any plastic. But the MK3 would be able to see that the filament had stalled and alert the user. The capabilities of the optical filament sensor represented a minor revolution in desktop 3D printing, and combined with the rest of the instrumentation in the MK3, promised to all but eradicate the heartbreak of failed prints.
Fast forward to February of 2019, and the announcement of the Prusa i3 MK3S. This relatively minor refresh of the printer collected up all the incremental tweaks that had been made during the production of the MK3, and didn’t really add any new features. Though it did delete one: the MK3S removed the optical encoder sensor used in the MK3, and with it the ability to sense filament movement. Users would have to decide if keeping the ability to detect clogs and tangles was worth giving up all of the other improvements offered by the update.
But why? What happened in those three years that made Prusa Research decide to abandon what promised to be a huge usability improvement for their flagship product? The answer is an interesting look at how even the cleverest of engineering solutions don’t always work as expected in the real-world.
Continue reading “The Prusa I3 MK3S And A Tale Of Two Sensors”
The B-Sides: Curious Uses Of Off-the-Shelf Parts
I admit: a few years of prototyping without easy machine shop access really whets my tastebuds for turning metal chips. But all that time spent away from proper machine tools has also pushed me to re-imagine part catalogs, something I see almost every day. Without any precision metalworking tools handy, stock mechanical parts have become my supplement for complexity. And so a former dogma to machine-everything-thyself has been transformed into a hunt for that already-made-part-that-does-it-for-you.
But with part catalogs featuring tens of thousands of purpose-built parts, I started reimagining some of them for other misdeeds. And after a few years spent reinventing use cases for some of these parts, I’m about ready to tell you how to misuse them properly. So today I’d like to show you some of my favorite mechanical part B-sides, so to speak. These are ordinary parts in unorthodox places–something you surely won’t find in the datasheet! Now let’s have a look. Continue reading “The B-Sides: Curious Uses Of Off-the-Shelf Parts”
CNC On The Desktop Hack Chat
Join us on Wednesday, August 26 at noon Pacific for the CNC on the Desktop Hack Chat with Matt Hertel and John Allwine!
Once limited to multi-million dollar machines on the floors of cavernous factories, CNC technology has moved so far downscale in terms of machine size that it’s often easy to lose track of where it pops up. Everything from 3D-printers to laser engravers use computer numeric control to move a tool to some point in three-dimensional space, and do it with unmatched precision and reproducibility.
CNC has gotten so pervasive that chances are pretty good that there’s a CNC machine of some sort pretty close to everyone reading this, with many of those machines being homebrew designs. That’s the backstory of Pocket NC, a company that was literally started in a one-bedroom apartment in 2011 by Matt and Michelle Hertel. After a successful Kickstarter that delivered 100 of their flagship five-axis desktop CNC mills to backers, they geared up for production and now turn out affordable machine tools for the masses. We’ve even seen some very complex parts made on these mills show up in projects we’ve featured.
For this Hack Chat, we’ll be joined by Pocket NC CTO and co-founder Matt Hertel and John Allwine, who recently joined the company as Principal Software Engineer. We’ll discuss not only Pocket NC’s success and future plans, but the desktop CNC landscape in general. Drop by with your questions regarding both the hardware and the software side of CNC, about turning an idea into a business, and where the CNC world and next-generation manufacturing will be heading in the future.
Our Hack Chats are live community events in the Hackaday.io Hack Chat group messaging. This week we’ll be sitting down on Wednesday, August 26 at 12:00 PM Pacific time. If time zones baffle you as much as us, we have a handy time zone converter.
Click that speech bubble to the right, and you’ll be taken directly to the Hack Chat group on Hackaday.io. You don’t have to wait until Wednesday; join whenever you want and you can see what the community is talking about.