A team of students in Antwerp, Belgium are responsible for Project Aslan, which is exploring the feasibility of using 3D printed robotic arms for assisting with and translating sign language. The idea came from the fact that sign language translators are few and far between, and it’s a task that robots may be able to help with. In addition to translation, robots may be able to assist with teaching sign language as well.
The project set out to use 3D printing and other technology to explore whether low-cost robotic signing could be of any use. So far the team has an arm that can convert text into finger spelling and counting. It’s an interesting use for a robotic arm; signing is an application for which range of motion is important, but there is no real need to carry or move any payloads whatsoever.
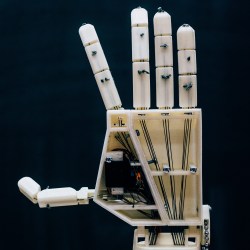
A single articulated hand is a good proof of concept, and these early results show some promise and potential but there is still a long ways to go. Sign language involves more than just hands. It is performed using both hands, arms and shoulders, and incorporates motions and facial expressions. Also, the majority of sign language is not finger spelling (reserved primarily for proper names or specific nouns) but a robot hand that is able to finger spell is an important first step to everything else.
Future directions for the project include adding a second arm, adding expressiveness, and exploring the use of cameras for the teaching of new signs. The ability to teach different signs is important, because any project that aims to act as a translator or facilitator needs the ability to learn and update. There is a lot of diversity in sign languages across the world. For people unfamiliar with signing, it may come as a surprise that — for example — not only is American Sign Language (ASL) related to French sign language, but both are entirely different from British Sign Language (BSL). A video of the project is embedded below.
Continue reading “3D Printed Robotic Arms For Sign Language”