Hobby servos are great, but they’re in many ways not ideal for robotic applications. The good news is that [Adam] brings the latest version of his ServoProject, providing off-the-shelf servos with industrial-type motion control to allow for much, much tighter motion tracking than one would otherwise be limited to.
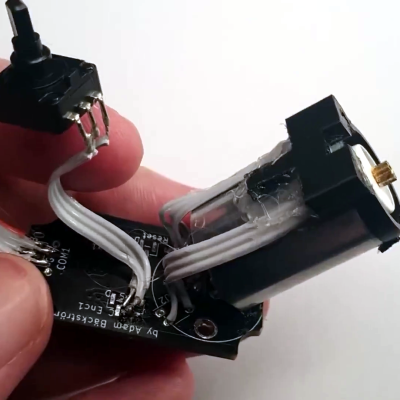
The PID control system in a typical hobby servo is very good at two things: moving to a new position quickly, and holding that position. This system is not very good at smooth motion, which is desirable in robotics along with more precise motion tracking.
[Adam] has been working on replacing the PID control with a more capable cascade-based control scheme, which can even compensate for gearbox backlash by virtue of monitoring the output shaft and motor position separately. What’s really new in this latest version is that there is no longer any need to perform surgery on the DC motor when retrofitting a servo; the necessary sensing is now done externally. Check out the build instructions for details.
The video (embedded just below) briefly shows how a modified servo can perform compared to a stock one, and gives a good look at the modifications involved. There’s still careful assembly needed, but unlike the previous version there is no longer any need to actually open up and modify the DC motor, which is a great step forward.
Continue reading “Vastly Improved Servo Control, Now Without Motor Surgery”