About a decade ago [Windell Oskay] and [Lenore Edman] spun out of Evil Mad Scientist Laboratories to work on CandyFab, an inexpensive 3D printer that used sugar as its medium. Wondering what happened to CandyFab? It’s been nearly that long since we last wrote about their work and Maker technology has moved on; nowadays 3D printers run the gamut from very inexpensive to production ready. The CandyFab project and nascent company are now shuttered, but there is a epilogue with some interesting lessons.
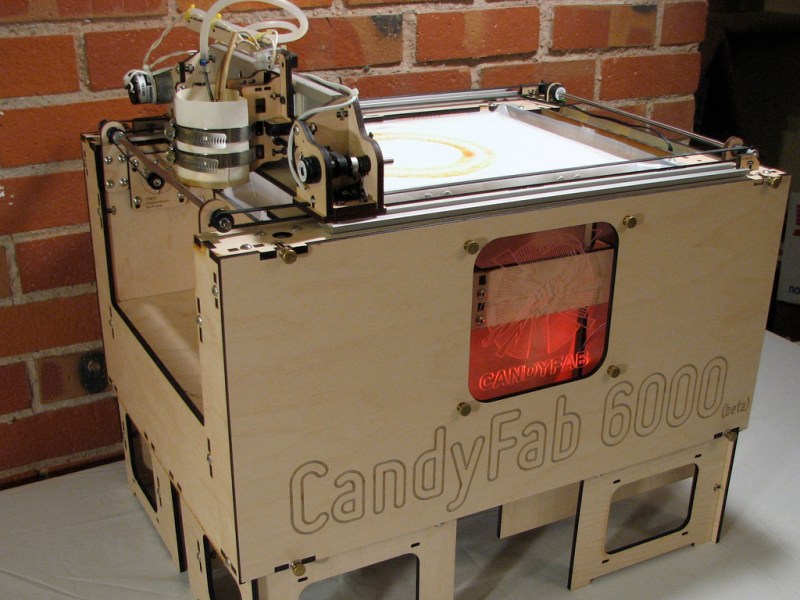
First of all, the saga of the CandyFab series of printers (above on the same page) is worth a read. Some of what these machines were capable of is still quite impressive by modern standards. Sure your Monoprice Mini Delta may be easy to use, fully assembled, functional when you take it out of the box, and quiet. But what if you need to print something up to 8.5″ x 11″ x 17″? The CandyFab 5000 can do that. Or even a humongous 24″ x 13.5″ x 9″? The CandyFab 4000 can do it, and for a measly $37 (if you printed a solid cube exactly the size of the build volume)! Sugar may have downsides but it’s still a pretty clever medium for some uses.
CandyFab credits the rise of MakerBot coupled with the complexity of iterating from a pile of “surplus junk” (their words) to something kitable. Reading their post-mortem brings to mind familiar problems from today’s hardware world. A spike of fantastic early publicity lead to the need to handle press while rapidly iterating from the aforementioned surplus parts to a reliable and manufacturable design. Then the complexity of balancing a day job and other side projects with the prospect of CandyFab as a business. Ultimately the need for the project in the first place (accessible inexpensive 3D printers) was alleviated by the market and the project came to a graceful close.
Give the post a read, we’re sure you’ll learn something!