[davemoneysign] designed this fascinating roller chain kinetic sculpture, which creates tumbling and unpredictable patterns and shapes as long as the handle is turned; a surprisingly organic behavior considering the simplicity and rigidity of the parts.
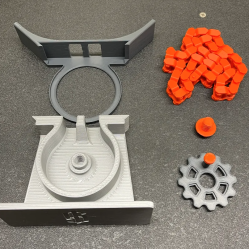
The inspiration for this came from [Arthur Ganson]’s Machine With Roller Chain sculpture (video, embeded below). The original uses a metal chain and is motor-driven, but [davemoneysign] was inspired to create a desktop and hand-cranked manual version. This new version is entirely 3D-printed, and each of the pieces prints without supports.
According to [davemoneysign], the model works well with a chain of 36 links, but one could easily experiment with more or fewer and see how that changes the results. Perhaps with the addition of a motor this design could be adapted into something like this chains-and-sprockets clock?
You can see [Arthur Ganson]’s original in action in the video embedded below. It demonstrates very well the piece’s chaotic and unpredictable — yet oddly orderly — movement and shapes. Small wonder [davemoneysign] found inspiration in it.
Continue reading “3D-Printable Sculpture Shows Off Unpredictable Order Of Chains”