When we say non-planar slicing is for the birds, we mean [Joshua Bird], who demonstrates the versatility of his new non-planar S4-Slicer by printing a Benchy upside down with the “Core R-Theta” printer we have featured here before.
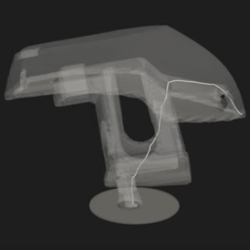
This non-planar slicer is built into a Jupyter notebook, which follows a relatively simple algorithm to automatically generate non-planar toolpaths for any model. It does this by first generating a tetrahedral mesh of the model and then calculating the shortest possible path through the model from any given tetrahedron to the print bed. Even with non-planar printing, you need to print from the print-bed up (or out).
Quite a lot of math is done to use these paths to calculate a deformation mesh, and we’ll leave that to [Joshua] to explain in his video below. After applying the deformation, he slices the resulting mesh in Cura, before the G-code goes back to Jupyter to be re-transformed, restoring the shape of the original mesh.
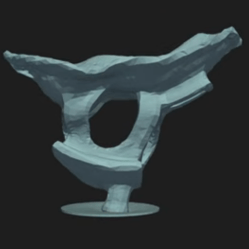
So yes, it is G-code bending as others have demonstrated before, but in a reproducible, streamlined, and straightforward workflow. Indeed, [Josh] credits much of the work to earlier work on the S^3-Slicer, which inspired much of the logic and the name behind his S4 slicer. (Not S4 as in “more than S^3” but S4 as a contraction of “Simplified S^3”). Once again, open source allows for incremental innovation.
It is admittedly a computationally intensive process, and [Joshua] uses a simplified model of Benchy for this demo. This seems exactly the sort of thing we’d like to burn compute power on, though.
This sort of non-planar 3D printing is an exciting frontier, one which we have covered before. We’ve seen techniques for non-planar infill, or even to print overhangs on unmodified Cartesian printers, but this is probably the first time we’ve seen Benchy given the non-planar treatment. You can try S4 slicer for yourself via GitHub, or just watch the non-planar magic in action after the break. Continue reading “Non-planar Slicing Is For The Birds”