Three years ago, [Enza3D] put together a 3D printed version of the Eye of Agamotto as seen in Marvel’s Doctor Strange. It was a good looking prop, but there was definitely some room for improvement in terms of screen accuracy and scale. With a new Strange film now in theaters, it seemed a good a time as any to revisit the design and tighten up some loose ends.
As you might expect for something that’s supposed to be magic, the internal mechanism required to get all of the moving parts going is quite complex. Not only does the iris need to open and close, but the rings need to spin at different speeds to recreate the effect seen in the film. Impressively, there’s not a single line of code or a microcontroller to be seen here — everything is done with a carefully designed set of a gears and a single N20 motor.
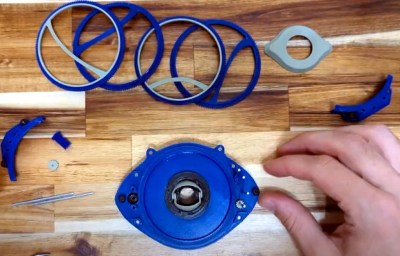
[Enza3D] tried to simplify the construction of the clockwork-like mechanism as much as possible compared to the earlier version, and made some nice improvements like unifying the size of the screws and shafts used in the assembly so there’s no danger of using the wrong part. Despite their size and fine pitch, all of the gears can be printed on a standard FDM desktop printer, in this case a Prusa Mini.
That said, [Enza3D] did switch over to resin prints for the outside of the prop. Incidentally, in another clever design decision, the outer ornamental case is completely separate from the internal powered mechanism. That lets you easily take the unit apart for maintenance or repairs without risking damage to your finish work. Check out the video after the break for a breakdown of how the device is assembled, as well as some tips on how to make shiny pieces of plastic look like aged metal.
Truth be told, if we were working on our own Doctor Strange cosplay, our first pick would still be the ridiculously awesome POV spellcasting gun we covered back in 2018 — but this beauty comes in at a close second for sure.
Continue reading “Taking Another Swing At A 3D Printed Eye Of Agamotto”