Dutch research institute [AMOLF] shows off a small robot capable of walking, hopping, and swimming without any separate control system. The limbs synchronize thanks to the physical interplay between the robot’s design and its environment. There are some great videos on that project page, so be sure to check it out.
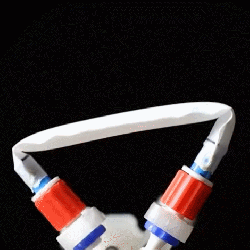
Powered by a continuous stream of air blown into soft, kinked tubular limbs, the legs oscillate much like the eye-catching “tube man” many of us have seen by roadsides. At first it’s chaotic, but the movements rapidly synchronize into a meaningful rhythm that self-synchronizes and adapts. On land, the robot does a sort of hopping gait. In water, it becomes a paddling motion. The result in both cases is a fast little robot that does it all without any actual control system, relying on physics.
You can watch it in action in the video, embedded below. The full article “Physical synchronization of soft self-oscillating limbs for fast and autonomous locomotion” is also available.
Gait control is typically a nontrivial problem in robotics, but it doesn’t necessarily require a separate control system. Things like BEAM robotics and even the humble bristlebot demonstrate the ability for relatively complex behavior and locomotion to result from nothing more than the careful arrangement of otherwise simple elements.
Continue reading “Behold Self-Synchronizing, Air-Flopping Limbs That Hop And Swim”