DOOM has been ported to a lot of platforms — to the point where the joke is kind of getting old now. Evidence of that is available in the fact that brands are now getting in on the action. Yes, as reported by The Register, you can now officially play DOOM on your Husqvarna’s Automower.
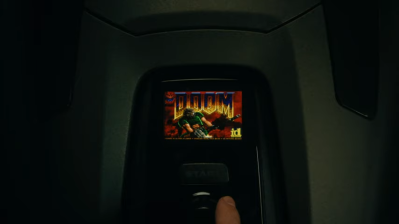
We had to check if this was some kind of joke; indeed, the April release date had us looking at the calendar. However, it seems to be legit. You’ll be able to download a version of DOOM via the Husqvarna Automower Connect App, and play it on the tiny screen of your robot lawnmower. Hilariously, due to the size of the game, Husqvarna notes it “may take up to a week before the game is playable” due to the time it takes the mower to download it, along with a necessary software update.
Controls are simple. The knob on the robot is used for turning left and right, while pressing start lets you run forward. Firing weapons is done by pressing the control knob.
We’ve seen some quality ports before, including an arcade port that was particularly cool. Really, though, at this stage, you have to work harder to impress. Show us DOOM running on a Minuteman launch console or something. Continue reading “DOOM Runs On Husqvarna’s Robot Lawnmower”