By pretty much any metric you care to use, the last couple of decades has been very good for the open source movement. There was plenty of pushback in the early days, back when the only people passionate about the idea were the Graybeards in the IT department. But as time went on, more and more developers and eventually companies saw the benefit of sharing what they were working on. Today, open source is effectively the law of the land in many fields, and you don’t have to look far to find the community openly denouncing groups who are keeping their source under lock and key.
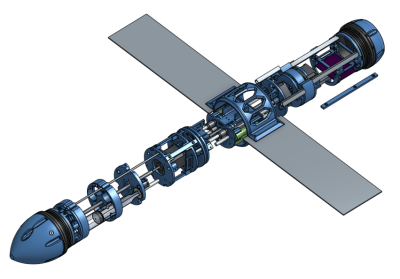
In the last few years, we’ve even seen the idea gain traction in the hardware field. While it’s not nearly as prevalent as opening up the software side of things, today it’s not uncommon to see hardware schematics and PCB design files included in project documentation. So not only can you download an open source operating system, web browser, and office suite, but you can also pull down all the information you need to build everything from a handheld game system to an autonomous submarine.
With so many projects pulling back the curtain, it’s not unreasonable to wonder where the limits are. There’s understandably some concerns about the emerging field of biohacking, and anyone with a decent 3D printer can download the files necessary to produce a rudimentary firearm. Now that the open source genie is out of the bottle, it seems there’s precious little that you can’t download from your favorite repository.
Scratching an exceptionally surprising entry off that list is Transatomic, who late last year uploaded the design for their TAP-520 nuclear reactor to GitHub. That’s right, now anyone with git
, some uranium, and a few billion dollars of seed money can have their very own Molten Salt Reactor (MSR). Well, that was the idea at least.
So six months after Transatomic dumped a little under 100 MB worth of reactor documentation on GitHub, is the world any closer to forkable nuclear power? Let’s find out.
Continue reading “You Wouldn’t Download A Nuclear Reactor, But Could You?”