Laser-engraving a cylindrical object usually requires a rotary attachment, which is a motorized holder that rotates a cylindrical object in sync with the engraver. But [Samcraft] shows that engraving all around a mug can be done without a motorized rotary holder.
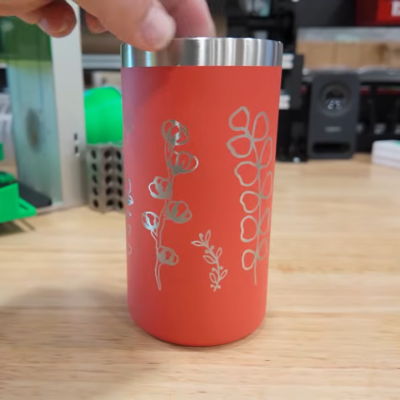
The basic idea is to split the design into a number of separate engraving jobs, each containing one element of the overall design, then setting the mug into a 3D printed jig and manually rotating it between jobs. To demonstrate, [Samcraft] selects a series of line-art flowers and plants which are ideal for this approach because there’s no need to minutely register the individual engravings with one another.
What about focus? [Samcraft] found that a design up to 45 mm wide could be engraved onto the curved surface of his mug before focus suffers too much. It’s true that this technique only works with certain types of designs — specifically those with individual elements that can be separated into tall and thin segments — but the results are pretty nice.
Laser engravers are a very serious potential eye hazard, and we are not delighted to see the way the shield around [Samcraft]’s engraver cannot close completely to accommodate the mug while the laser is active. But we’re going to assume [Samcraft] has appropriate precautions and eye protection in place off-camera, because laser radiation and eyeballs absolutely do not belong together, even indirectly.
Continue reading “Engrave A Cylinder Without A Rotary Attachment? No Problem!”