Learning anything new, especially so broad and far reaching as electronics, can be hard. [IMSAI Guy] knows this because he gets asked regularly “how do I learn electronics?” Many of you reading this will have a few ideas to pass along (and we encourage you to share your take on it in the comments below) but there is an even greater number of people who are asking the same question, and [IMSAI Guy]’s take on it is one that this particular Hackaday writer can relate to.
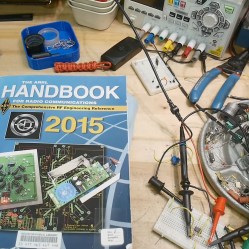
According to [IMSAI Guy], an excellent place to start is the ARRL Handbook. The ARRL Handbook is an electronics and RF engineering guide published by the Amateur Radio Relay League in the US. It’s a wonderful reference, and past editions can be had very inexpensively and are every bit as handy. Many hams will have a copy they could be talked out of, and you can likely find one at your local library. Where to start in the Handbook, then?
[IMSAI Guy] recommend starting with whatever catches your fancy. As an example, he starts with Op Amps, and rather than diving straight into the math of how they work or even worrying to much about what they are- he just builds a circuit and then plays with it to intrinsically understand how it works, a “learn by doing” approach that he has found extremely helpful just as many of us have. We also appreciated is very straightforward approach to the math: Don’t bother with it unless you need to for some reason, and definitely don’t start by learning it first.
In fact, that same reasoning is applied to any subject: Learn it as you need it, and don’t start by learning but rather by doing. The learning will come on its own! Be sure to check out the entire video and let us know what you think, and how you approached learning electronics. Thanks to [cliff] for the great Tip!