[Eric Berger] has a thoughtful and detailed article explaining why Ingenuity, NASA’s small helicopter on Mars, was probably far more revolutionary than many realize, and has a legacy to grant the future of off-world exploration that is already being felt.
Ingenuity was recently grounded due to rotor damage, having already performed far beyond the scope of its original mission. The damage, visible by way of a shadow from one of the rotors, might not look like much at first glance, but flying in the vanishingly-thin atmosphere of Mars requires the 1.18 meter (3.9 foot) carbon fiber blades to spin at very high speeds — meaning even minor rotor damage could be devastating.
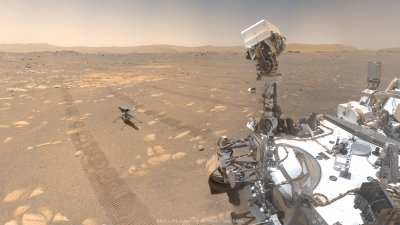
[Eric] points out a lot that is deeply interesting and influential about Ingenuity. Not only is successful powered flight on another planet a real Wright brothers moment, but how Ingenuity came to be validates a profoundly different engineering approach for NASA.
To work in the space industry is to be constrained by mass. But even so, Ingenuity‘s creators had a mere four pounds to work with. That’s for rotors, hardware, electronics, batteries, solar panel — all of it. NASA’s lightest computer module alone weighed a pound, so engineers had no choice but to depart from the usual NASA way of doing things to get it done at all. Not everyone at NASA was on board. But Ingenuity worked, and it worked wonderfully.
Powered flight opens new doors, and not just for support roles like navigation planning. There’s real science that can be done if powered flight is on the table. For example, [Eric] points out that inaccessible terrain such as the Valles Marineris canyon on Mars is doubtlessly scientifically fascinating, but at 4,000 km long and up to 7 km deep, rover-based exploration is not an option.