Thus far, the majority of electric cars on sale have been aimed at commuters, fitting into the sedan and SUV segments of the marketplace. Going forward, there’s a very real need for electrification to touch the whole spectrum of automobiles, and that includes work vehicles like pickup trucks. A company called Magna have recently thrown their hat into the ring in just this space, developing a simple drivetrain that can be readily installed in pickup trucks without major modifications. Continue reading “Magna Announces Simple Drive Solution For Electric Pickup Trucks”
Gaming With 1 Horsepower Of Rumble Feedback
Force feedback took off in a big way in the late 90s, bringing a sense of realism to flight sticks and racing wheels that hadn’t been there before. Its cheaper haptic cousin was rumble feedback via vibration motors, which does add a little something but it’s more an idea of a feeling than anything relevant to real life. It’s also usually pretty weak, but [teenenggr] has a way around that.
The build takes a regular Playstation controller, and disconnects the internal rumble motors. The controller’s motor output is instead linked to an Arduino Uno’s digital input. When the Arduino detects the rumble motor signal switching on, it turns on a relay, supplying power to a hefty one horsepower induction motor, fitted with an eccentric weight.
What happens next is pure chaos. Essentially equivalent to throwing a brick in a washing machine, the motor shakes the entire desk at the slightest hint of rumble signals from the gain. Sustained vibration commands, such as when firing machine guns in Crysis, flung [teenenggr]’s monitor from the desk. Even with it taped down, game play quickly became impossible as he inadvertently hits ALT-Tab and leaves the game while trying to hang on to the desk for dear life.
Is it a useful hack? No, but it would make an excellent prank if bolted underneath your friend’s gaming rig for a laugh. With that said, the intense vibration probably won’t do any good for mechanical hard drives, anything with edge connectors, or just their computer in general. It’s a big step up from the last [teenenggr] project we featured – a rumble feedback mouse. Video after the break.
Continue reading “Gaming With 1 Horsepower Of Rumble Feedback”
Sanity Check Your Engines With This Dynamometer
As you get ready to pop the hood of your RC car to drop in a motor upgrade, have you ever wondered how much torque you’re getting from these small devices? Sure, we might just look up the motor specs, but why trust the manufacturer with such matters that you could otherwise measure yourself? [JohnnyQ90] did just that, putting together an at home-rig built almost from a stockpile of off-the-shelf parts.
To dig into the details, [JohnnyQ90] has built himself a Prony Brake Dynamometer. These devices are setup with the motor shaft loosely attached to a lever arm that can push down on a force-measuring device like a scale. With our lever attached, we then power up our motor. By gradually increasing the “snugness” of the motor shaft, we introduce sliding friction that “fights” the motor, and the result is that, at equilibrium, the measured torque is the maximum amount possible for the given speed. Keep turning up that friction and we can stall the motor completely, giving us a measurement of our motor’s stall torque.
Arming yourself with a build like this one can give us a way to check the manufacturer’s ratings against our own, or even get ratings for those “mystery motors” that we pulled out the dumpster. And [JohnnyQ90’s] build is a great reminder on how we can leverage a bit of physics and and a handful of home goods to get some meaningful data.
But it turns out that Prony Brake Dynamometers aren’t the only way of measuring motor torque. For a disc-brake inspired, have a look at this final project. And if you’re looking to go bigger, put two motors head-to-head to with [Jeremy Felding’s] larger scale build.
Continue reading “Sanity Check Your Engines With This Dynamometer”
A Lot Of Effort For A Pi Laptop
Building a Raspberry Pi laptop is not that uncommon. In fact, just a few clicks from any of the major electronics suppliers will have the parts needed for such a project speeding on their way to your house in no time at all. But [joekutz] holds the uncontroversial belief that the value in these parts has somewhat diminishing returns, so he struck out to build his own Pi laptop with a €4 DVD player screen and a whole lot of circuit wizardry to make his parts bin laptop work.
The major hurdle that he needed to overcome was how to power both the display and the Pi with the two small battery banks he had on hand. Getting 5V for the Pi was easy enough, but the display requires 8V so he added one lithium ion battery in series (with its own fuse) in order to reach the required voltage. This does make charging slightly difficult but he also has a unique four-pole break-before-make switch on hand which doesn’t exactly simplify things, but it does make the project function without the risk of short-circuiting any of the batteries he used.
The project also makes use of an interesting custom circuit which provides low voltage protection for that one lonely lithium battery as well. All in all it’s a master course in using some quality circuit-building skills and electrical theory to make do with on-hand parts (and some 3D printing) rather than simply buying one’s way out of a problem. And the end result is something that’s great for anything from watching movies to playing some retro games.
Treatment Triggers Teeth To Thrive
We humans like to think we’re pretty advanced, but we can’t regrow missing teeth in adulthood like sharks, alligators, and crocodiles. Once those pearly whites are gone, they’re gone for good, and we don’t even have a way to regenerate the protective enamel. However, this may not always be the case, because scientists at Kyoto University and University of Fukui in Japan have discovered a monoclonal antibody treatment that triggers tooth regeneration in laboratory mice.
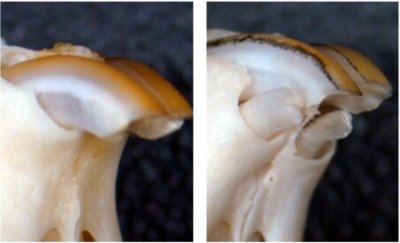
Monoclonal antibodies are lab-fabbed molecules that act as substitute antibodies to enhance the body’s natural defenses against diseases like cancer and arthritis. These antibodies are also used to develop vaccines and treat COVID-19. In the case of cancer, monoclonal antibodies bind to antigens on cancer cells, effectively flagging them for removal, but they also do much more, such as deliver chemo and radioimmunotherapies.
By blocking the gene USAG-1, the scientists saw an increase in Bone Morphogenic Protein (BMP), which is a molecule that dictates the number of teeth a given creature will have in the first place. Because of this increase in BMP, the mice were able to regrow teeth. This proposition was a challenging one — BMP affects other aspects of development, and the early attempts did more harm than good by causing birth defects. The good news is that the treatment also worked in ferrets, whose teeth are much closer to human dentition than mice. Before moving on to human trials, the scientists will test it out on pigs and dogs. If you were given a second shot at a set of teeth, would you treat them better than the first, or even worse because you can just grow new ones again?
Speaking of pigs, it seems that pig-to-human organ transplants are on track for 2021.
Garage Door Controller Gets The IoT Treatment
[TheStaticTurtle] built a custom controller for automating his garage doors. He wanted to retain the original physical button and RF remote control interfaces while adding a more modern wireless control accessible from his internet connected devices. Upgrading an old system is often a convoluted process of trial and error, and he had to discard a couple of prototype versions which didn’t pan out as planned. But luckily, the third time was the charm.
The original door-closer logic was pretty straightforward. Press a button and the door moves. If it’s not going in the desired direction, press the button once again to stop the motor, and then press it a third time to reverse direction. With help from the user manual diagrams and a bit of reverse-engineering, he was able to get a handle on how to plan out his add-on controller to interface with the old system.
There are many micro-controller options available these days when you want to add IoT to a project, but [TheStaticTurtle] decided to use the old faithful ESP8266 as the brains of his new controller. For his add-on board to work, he needed to detect the direction in which the motor was turning, and detect the limit switches when the door reached end of travel in either direction. Finally, he needed a relay contact in parallel with the activation button to send commands remotely.
To sense if the motor was moving in the “open” or “close” direction, he used a pair of back-to-back opto-couplers in parallel with the motor terminals. He connected another pair of opto-couplers across the two end-limit switches which indicated when the door was fully open or closed, and shut off the motor supply. Finally, a GPIO from the ESP8266 actuates a relay to send the door open and close commands. The boards were designed in EasyEDA and with a quick turnaround from China, he was able to assemble, test and debug his boards pretty quickly.
The code was written using the Arduino IDE and connects the ESP8266 to the MQTT server running on his home automation computer. The end result is a nice dashboard with three icons for open, close and stop, accessible from all the devices connected to his home network. A 3D printed enclosure attaches outside the original control box to keep things tidy. Using hot melt glue as light pipes for the status LED’s is a pretty nifty hack. If you are interested in taking a deeper look at the project, [TheStaticTurtle] has posted all resources on his Github repository.
Homebrew RISC-V Computer Has Beauty And Brains
Building your own CPU is arguably the best way to truly wrap your head around how all those ones and zeros get flung around inside of a computer, but as you can probably imagine even a relatively simple processor takes an incredible amount of time and patience to put together. Plus, more often than not you’re then left with a maze of wires and perfboards that takes up half your desk and doesn’t do a whole lot more than blink some LEDs.
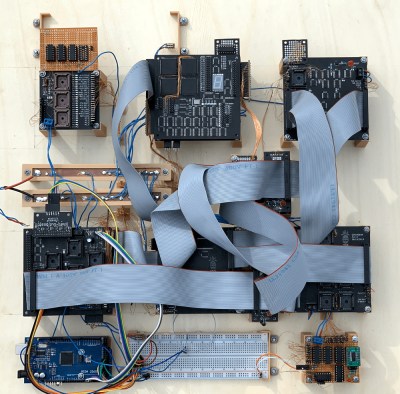
But the Pineapple ONE, built by [Filip Szkandera] isn’t your average homebrew computer. Oh sure, it still took two years for him to design, debug, and assemble, his 32-bit RISC-V CPU and all its associated hardware; but the end result is a gorgeous looking machine that runs C programs and offers a basic interactive shell over VGA. In fact with its slick 3D printed enclosure, vertically stacked construction, and modular peripheral connections, it looks more like some kind of high-tech scientific instrument than a computer; homebrew or otherwise.
[Filip] says he was inspired to build this 500 kHz (yes, kilohertz) beauty using only discrete logic components by [Ben Eater]’s well known 8-bit breadboard computer and [Robert Baruch]’s LMARV-1 (Learn Me A RISC-V, version 1). He spent six months simulating the machine before he even started creating the schematics, let alone design the individual boards. He tried to keep all of his PCB’s under 100 x 100 mm to take advantage of discounts from the fabricator, which ultimately led to the decision to align the nine boards vertically and connect them together with pin headers.
In the video below you can see [Filip] start up the computer, call up a bit of system information, and even play a rudimentary game of snake before peeking and poking some of the machine’s 512 kB of RAM. It sounds like there’s still some work to be done and bugs to squash, but we’ve already seen enough to say this machine has more than earned entry into the pantheon of master-crafted homebrew computers.
Continue reading “Homebrew RISC-V Computer Has Beauty And Brains”