Air conditioners are easy to take for granted. From refrigerators to climate control, most of us would miss them dearly if they disappeared. That’s part of what draws [Josh Levine]’s interest in air conditioners, and he has provided an interesting tour of several different units and how different they can be, despite all working in basically the same way.
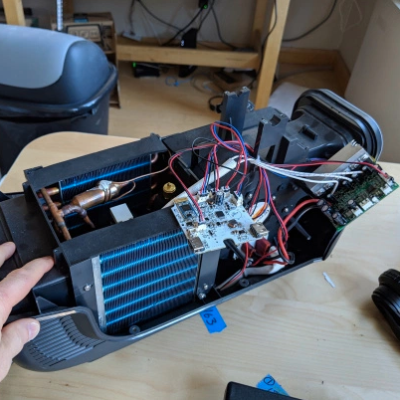
One way that air conditioners try to stand out is by being quiet, and the bulk of noise comes from the fans and the compressor. One unit (the Haier Serenity) aimed to be the quietest unit possible, but while this effort had mixed results at best it is still interesting to see [Josh] give a tour of the different ways they tried to reduce noise (YouTube, embedded below). Noise-limiting elements include the unusual step of using separate motors for the indoor and outdoor fans, and even little counterweights to ensure they are perfectly balanced, just like wheel weights on automobile tires.
Another notable air conditioner is the Zero Breeze, a portable unit that was the product of a Kickstarter campaign. Features included (either bizarrely or predictably, you be the judge) a bluetooth speaker and an LED flashlight. [Josh] more than half suspected the product would never actually ship, but was pleasantly surprised. Not only did it deliver, it turned out to be a pretty nice design with only a couple of mildly head scratching moments (YouTube, also embedded below).
There are a few more to check out in the roundup on [Josh]’s web site, which he also compares and contrasts with his own DIY unit which we featured in the past.
Continue reading “See How Wildly Different Air Conditioners Can Be (On The Inside)”