Good news this week from the Sun’s far side as the Parker Solar Probe checked in after its speedrun through our star’s corona. Parker became the fastest human-made object ever — aside from the manhole cover, of course — as it fell into the Sun’s gravity well on Christmas Eve to pass within 6.1 million kilometers of the surface, in an attempt to study the extremely dynamic environment of the solar atmosphere. Similar to how manned spacecraft returning to Earth are blacked out from radio communications, the plasma soup Parker flew through meant everything it would do during the pass had to be autonomous, and we wouldn’t know how it went until the probe cleared the high-energy zone. The probe pinged Earth with a quick “I’m OK” message on December 26, and checked in with the Deep Space Network as scheduled on January 1, dumping telemetry data that indicated the spacecraft not only survived its brush with the corona but that every instrument performed as expected during the pass. The scientific data from the instruments won’t be downloaded until the probe is in a little better position, and then Parker will get to do the whole thing again twice more in 2025. Continue reading “Hackaday Links: January 5, 2025”
Reverse-Engineering The Polynomial Constants In The Pentium’s FPU
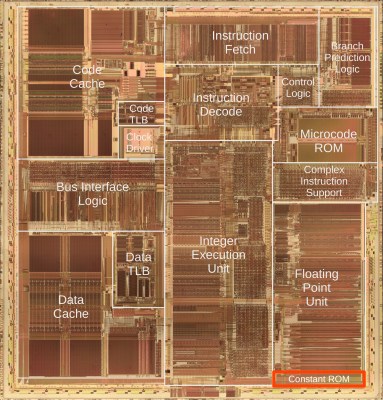
Released in 1993, Intel’s Pentium processor was a marvel of technological progress. Its floating point unit (FPU) was a big improvement over its predecessors that still used the venerable CORDIC algorithm. In a recent blog post [Ken Shirriff] takes an up-close look at the FPU and associated ROMs in the Pentium die that enable its use of polynomials. Even with 3.1 million transistors, the Pentium die is still on a large enough process node that it can be readily analyzed with an optical microscope.
In the blog post, [Ken] shows how you can see the constants in each ROM section, with each bit set as either a transistor (‘1’) or no transistor (‘0’), making read-out very easy. The example looks at the constant of pi, which the Pentium’s FPU has stored as a version with no fewer than 67 significand bits along with its exponent.
Continue reading “Reverse-Engineering The Polynomial Constants In The Pentium’s FPU”
Stacy’s Computer Has Got It Going On
According to [ClassicHasClass], the best way to open an Atari Stacy is to not open an Atari Stacy. Apparently, these old computers were not pleasant to work on. The cables were not keyed and were prone to short against things. Screws easily strip out plastic holes. Of course, there wouldn’t be a story if there wasn’t a teardown and an upgrade that you can check out in the post.
The Stacy was one of Atari’s earliest portable systems and the first ST portable (that is, STacy). There’s a backlit LCD, a keyboard and trackball, and the usual ports. You could make do with a single floppy or spring for a second floppy or an internal SCSI hard drive. The 8 MHz 68000-based machine would set you back north of $2,300 back in 1989.
The original plan was to run the thing on C-cell batteries, but that would give you about 15 minutes of operation. They finally decided it was a luggable — you’d have to plug it into the wall. The battery compartment was there, but empty and glued shut.
Apparently, there were about 35,000 of these made, but they seem somewhat rare. But we do like a rare retrocomputer. Or even some that aren’t so rare.
Atari 65XE In Laptop Form
For better or worse, Atari is no longer a household name in computing, but for a time in the 1980s, it was a huge mover in the industry. They not only produced PCs but also a huge number of video game consoles. Although they were a major contributor to the video game crash of the 1980s, they managed to limp along a few more years afterward and produce some interesting machines in the following years, even though they weren’t ultimately able to compete with Nintendo or Sega. One of those computers from that era was a PC-console hybrid of sorts called the Atari XE, and [Sideburn] was able to turn one into a laptop.
The retro laptop began life as an Arabic PAL version of the 65XE, the PC version of the ubiquitous 65-series computer. A large portion of the computer was reworked, including the removal of the power supply in favor of a rechargeable battery with a 6-hour life. Also among the list of scrapped components was the video and sound connectors as well as the RF modulator, which would have been common for displays at the time, but this laptop is getting a 1920×1080 LCD panel to replace all of that old hardware. A 1MB memory upgrade, new speakers and amp, a WiFi card, and an SD floppy card emulator round out the build.
The final part of the build is assembling it all into a custom 3D printed case, and the resulting laptop that [Sideburn] calls the XE Book is a faithful adaptation of this niche computer into what could have been a laptop we would have seen in the late 80s or early 90s similar to the Toshiba T3200SXC. It matches the original’s footprint and still uses all of the core components, so it’s not too difficult to imagine something like this having existed in the past.
16-bit Linux-like Goodness
We see many 16-bit retrocomputers around here based on Intel and Intel-like chips such as the 8086, 8088, V20, and similar. While they don’t seem very powerful by today’s standards, they were perfectly capable machines and, thanks to Elks (Embeddedable Linux Kernel Subset), you can run something fairly Linux-like on these devices.
The requirements are light: 512K of RAM is desirable, but you can do something with 256K. If you have ROM, you can even get by with 128K. Most importantly, the system doesn’t require a memory management unit to remap memory like many operating systems.
E-Bike Motor Gets New Life As Hydro Plant
For economic reasons, not every lake with a dam can support a hydroelectric power plant. Some rivers or creeks are dammed for flood control or simply for recreation, and don’t have the flow rate or aren’t deep enough to make the investment of a grid-scale generation facility worthwhile. But for those of us with a few spare parts around and access to a small lake, sometimes it’s possible to generate a usable amount of energy with just a bit of effort.
[Beyond the Tint] is building this mostly as a proof-of-concept, starting with a 1,000W hub motor from an e-bike that’s been removed from its wheel. A 3D-printed waterwheel attachment is installed in its place, and the fixed shaft is attached to a homemade ladder-looking mechanism that allows the entire generator to be lowered into the flow of a moving body of water, in this case, a small stream. A bridge rectifier converts the AC from the hub motor (now a generator) into DC, and after a few measurements and trials, [Beyond the Tint] produced over 30W with the first prototype.
A second prototype was made with feedback from the first video he produced, this time with an enclosed paddlewheel. This didn’t appear to make much difference at first, but a more refined impeller may make a difference in future prototypes. Small-scale hydropower is a fairly popular challenge to tackle, especially in the off-grid community. With access to even a small flowing stream and enough elevation change, it’s possible to build something like this generator out of parts from an old washing machine.
Continue reading “E-Bike Motor Gets New Life As Hydro Plant”
All Aboard The Hack Train: Nottingham’s LED Revival
Hackerspaces are no strangers to repurposing outdated tech, and Nottingham Hackspace happens to own one of those oddities one rarely gets their hands on: a railway departure board. Left idle for over a decade, it was brought back to life by [asjackson]. Originally salvaged around 2012, it remained unused until mid-2024, when [asjackson] decided to reverse-engineer it. The board now cycles between displaying Discord messages and actual train departures from Nottingham Railway Station every few minutes. The full build story can be found in this blog post.
The technical nitty-gritty is fascinating. Each side of the board contains 4,480 LEDs driven as two parallel chains. [asjackson] dove into its guts, decoding circuits, fixing misaligned logic levels, and designing custom circuit boards in KiCAD. The latest version swaps WiFi for a WizNet W5500 ethernet module and even integrates the Arduino Uno R4 directly into the board’s design. Beyond cool tech, the display connects to MQTT, pulling real-time train data and Discord messages via scripts that bridge APIs and custom Arduino code.
This board is a true gem for any hackerspace, even more so now it’s working. It waited for the exact mix of ingredients why hackerspaces exist in the first place: curiosity, persistence, and problem-solving. Nottingham Hackspace is home to a lot more, as we once wrote in this introductory article.If you don’t have room for the real thing, maybe set your sights a bit smaller.
Do you have a statement piece this cool in your hackerspace or your home? Tip us!
Continue reading “All Aboard The Hack Train: Nottingham’s LED Revival”